Are you frustrated by rising production costs? Worried about poor casting quality, high waste rates, or unreliable suppliers? Struggling to find a process that balances affordability, sustainability, and performance?
Green sand casting may be the smart and eco-friendly solution you’ve been looking for. This time-tested metal casting method combines low-cost operation with consistent output, all while minimizing environmental impact. It’s ideal for those seeking a balance between tradition, efficiency, and ecological responsibility.
Whether you’re a seasoned professional or just entering the world of metal fabrication, this guide will walk you through everything you need to know about green sand casting—from its core benefits to key materials, techniques, and expert tips. Let’s explore why it remains one of the most powerful tools in modern manufacturing.
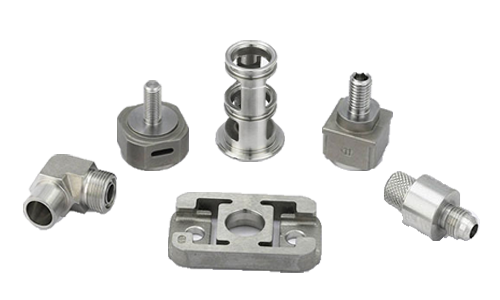
Get a quote now!
What Is Green Sand Casting?
Definition and Core Principles
Green sand casting is a time-honored and widely used metal casting method that involves creating molds from a damp, reusable mixture of sand, clay, and water. The term “green” does not refer to color, but rather to the moisture content of the mold, indicating that it hasn’t been cured or dried with heat. This technique forms the foundation of many modern foundry operations due to its simplicity, low cost, and remarkable efficiency.
In the world of metal fabrication, green sand casting has proven itself as a practical, versatile, and scalable process. Whether producing a single prototype or thousands of cast parts for industrial use, this method supports a wide range of metals—particularly iron, aluminum, and steel alloys.
Used in everything from agricultural machinery to automotive housings, green sand mold casting continues to dominate thanks to its adaptability, material savings, and fast production cycle. It remains especially attractive to manufacturers seeking an affordable yet high-quality approach to metal casting.
Why Is It Called “Green” Sand?
One of the most common questions asked by beginners is: Why is it called green sand?
The answer is simple. “Green” refers to the natural, uncured state of the sand used in mold preparation. Unlike other casting methods that require resin-bonded or baked molds, green casting sand maintains moisture and pliability throughout the molding process. This allows the sand to be reused multiple times after proper conditioning, making it more cost-effective and environmentally friendly.
The green sand for metal casting is not inherently environmentally “green,” but its reusability and non-toxic ingredients (typically silica sand and bentonite clay) align closely with sustainable manufacturing practices—a core concern in today’s global supply chain.
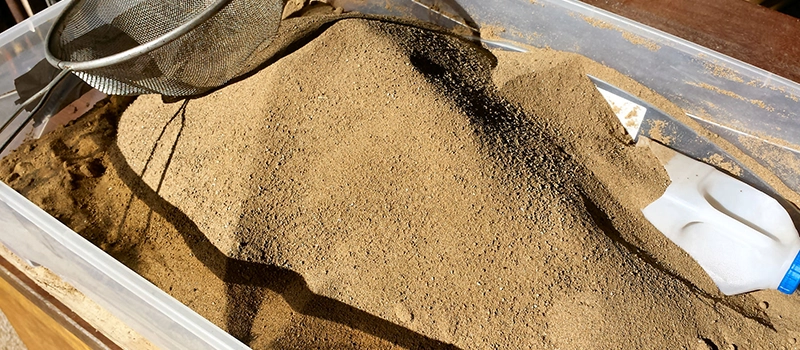
History and Evolution of the Method
Green sand casting has been used for centuries—dating back to ancient China and Egypt—where early blacksmiths and craftsmen shaped molten metal using damp sand molds. Over time, the process was refined through the Industrial Revolution, and later automated for mass production in foundries.
Today, green sand casting is still a key pillar of modern metal manufacturing. Its widespread use across North America, Europe, Japan, and Southeast Asia is due to its ability to accommodate high-volume production without the high tooling costs associated with more complex methods like die casting or investment casting.
With the rise of eco-friendly manufacturing and cost-sensitive procurement models, green sand mold casting is experiencing renewed relevance. It offers a balance between low environmental impact, consistent casting results, and operational flexibility—a trifecta that appeals to today’s industrial buyers and metalworking professionals.
Why Is Green Sand Used in Casting?
Environmental Benefits of Green Sand Casting
Need Help? We’re Here for You!
In today’s manufacturing world, environmental responsibility is no longer optional—it’s essential. That’s one of the key reasons green sand casting is used so widely in metalworking industries.
Unlike synthetic or chemically bonded mold systems, green sand in casting is composed primarily of natural materials: silica sand, bentonite clay, and water. These components are non-toxic, easy to handle, and, most importantly, recyclable. In many modern foundries, green sand can be reconditioned and reused over 20 times, reducing raw material waste and cutting down landfill contributions significantly.
Even better, the energy consumption in green sand casting is much lower compared to alternative methods like die casting or ceramic mold casting, which require higher temperature cycles or longer curing times. This energy efficiency translates directly into a lower carbon footprint—a growing priority for companies aiming to meet environmental regulations or corporate sustainability goals.
Recyclability of Green Sand
One of the standout benefits of green sand for casting is its reusability without toxic residue. After each pour, the used sand is cooled, screened, rehydrated, and conditioned back into production. This process requires minimal additives and results in significant cost savings, especially for high-volume production lines.
The clay and moisture content can be monitored and adjusted automatically in advanced foundries. This ensures that the green sand mold retains its ideal balance of strength and flexibility for repeat casting cycles. Over time, even the most basic workshop can build a closed-loop system to recycle casting sand, aligning casting operations with eco-friendly and waste-minimization goals.
Economic Advantages of Green Sand Casting
It’s not just about sustainability—green sand casting is also a clear winner when it comes to cost control.
- Tooling and setup costs for green sand molds are much lower than for high-pressure die casting.
- The mold preparation process is faster, reducing downtime between cycles.
- Green sand materials (silica, bentonite) are widely available and relatively inexpensive.
For manufacturers or suppliers managing tight margins, especially in developing country sourcing models like those used in China and Vietnam, green sand casting offers a balance of affordability and scalability that’s hard to beat.
Even for small-scale or startup manufacturers, this method lowers the entry barrier by eliminating the need for expensive molding equipment or long mold-curing times. Whether you’re making 100 parts or 100,000, the cost-per-part stays competitively low, making green sand casting an attractive option for global buyers.
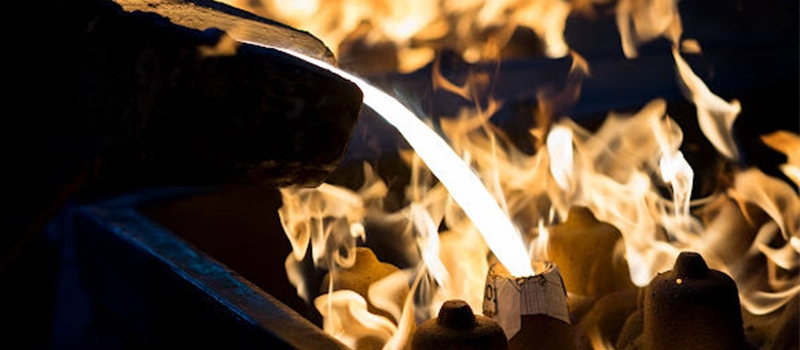
What’s Inside Green Casting Sand?
Main Components of Green Sand
At the heart of green sand casting is the mold—and the quality of that mold depends entirely on the materials that go into it. Despite its simplicity, green sand is a highly engineered mixture designed to deliver both flexibility and strength during the casting process.
The standard green casting sand recipe includes the following ingredients:
- Silica Sand (85–95%)
This is the base material. It provides structure and thermal resistance. The grain size, shape, and distribution affect the permeability and surface quality of the final casting. - Bentonite Clay (5–10%)
Bentonite acts as the binder. When mixed with water, it forms a plastic mass that holds the sand particles together. This ensures mold strength and dimensional stability. - Water (2–4%)
Moisture activates the clay and gives the sand its “green” or uncured state. Too little water, and the mold crumbles; too much, and it loses integrity. - Additives (up to 5%)
These include sea coal (finely ground bituminous coal), starch, or wood flour. They improve surface finish, reduce defects, and help the mold break away cleanly after cooling.
This balanced combination results in a mold that can withstand molten metal, maintain shape, and still be easily shaken out and reused.
Need Help? We’re Here for You!
Customizing Green Sand for Different Applications
Depending on the type of metal being poured or the complexity of the casting, the green sand mixture can be adjusted for performance.
For example:
- Aluminum green sand castings typically require finer grain sand for better surface finish and dimensional accuracy. Because aluminum pours at a lower temperature, sand burnout is less of a concern, so additives can be minimized.
- Green sand iron casting, by contrast, uses a slightly coarser sand and higher levels of additives like sea coal. This reduces the risk of metal penetration into the mold and improves surface integrity.
In high-performance applications—like automotive components or structural hardware—it’s essential to monitor the active clay content, moisture percentage, and grain size of the sand regularly. Even slight variations can lead to casting defects, poor surface quality, or mold failure.
That’s why many advanced foundries today use automated sand testing systems to analyze these properties in real time, ensuring consistent quality from batch to batch.
Eco-Friendly Aspects of Material Selection
Another reason green sand for metal casting is so appealing is its non-toxic and recyclable material base. Unlike synthetic resin-bonded sands, green sand doesn’t release harmful fumes when exposed to molten metal. This makes it safer for workers, reduces air pollution, and simplifies exhaust ventilation requirements.
Furthermore, because green sand can be recycled on-site and reshaped without the need for baking or curing, it consumes less energy and generates less waste over its lifecycle. This aligns with global environmental regulations and the growing demand for green manufacturing certifications in both local and export markets.
In short, the contents of green casting sand may seem simple—but they form the backbone of one of the most sustainable casting technologies still in use today.
Step-by-Step Green Sand Casting Process
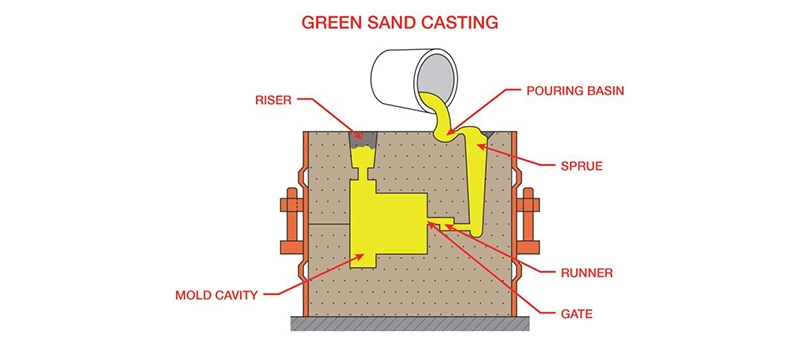
Mold Preparation: Laying the Foundation
Every successful green sand casting begins with the creation of a well-formed mold. The process starts by placing a pattern—a physical replica of the final part—into a molding box called a flask. This flask is then filled with the green sand mixture, compacted tightly to capture the shape and surface details of the pattern.
Patterns can be made from wood, metal, or plastic, depending on production volume and the required finish. The better the pattern quality, the better the final surface of the casting.
Once packed, the pattern is carefully removed, leaving behind a negative cavity that will be filled with molten metal. A gating system (pouring basin, runner, riser, etc.) is also created at this stage to allow metal to flow in and gases to escape.
Pattern Making: Accuracy Starts Here
The precision of the casting depends largely on the design and tolerance of the pattern. For high-accuracy parts like automotive housings or machine brackets, patterns are often machined using CNC equipment.
Important factors in pattern design include:
- Shrinkage allowance (to compensate for metal contraction)
- Draft angles (to aid in mold removal)
- Surface smoothness (to minimize finishing work)
Modern pattern shops use 3D modeling software and rapid prototyping tools to create accurate, repeatable patterns that optimize both sand packing and metal flow.
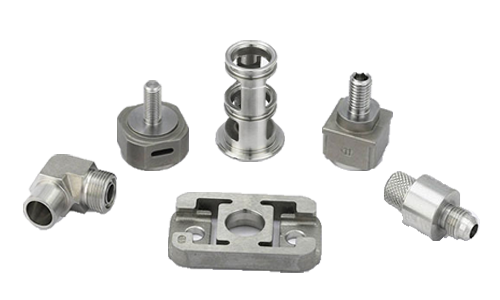
Get a quote now!
Metal Melting and Pouring: Precision in Action
Once the mold is ready, it’s time to melt the metal. Whether it’s iron, aluminum, or steel, the choice of material affects not only the melting point but also mold preparation and venting needs.
Molten metal is poured into the mold through the gating system using ladles. Timing and temperature are critical here. Pouring too hot can burn the mold and cause casting defects like rough surfaces or gas porosity; too cold, and the metal may solidify before completely filling the mold, leading to misruns.
Foundries often use temperature probes and real-time pouring control systems to ensure accuracy, especially for aluminum green sand castings, which have tighter thermal tolerances.
Cooling and Shakeout: Timing Is Everything
After pouring, the mold is left to cool and solidify. The cooling time depends on:
- Type of metal
- Thickness of casting walls
- Size of the mold cavity
Premature shakeout can cause warping or cracking, especially in green sand iron castings. Once the part has fully solidified, the mold is broken open and the casting is removed—a process known as shakeout.
The spent sand is then screened, cooled, and returned to the preparation unit for conditioning and reuse.
Cleaning, Finishing, and Inspection
After shakeout, the raw casting still has excess material, rough edges, and remnants of the gating system. These are removed through processes like:
- Fettling (cutting off runners and risers)
- Grinding or shot blasting (to improve surface finish)
- Machining (to achieve precise dimensions, if needed)
Next comes quality control, where the part is inspected for:
- Dimensional accuracy
- Surface integrity
- Internal defects (via ultrasonic or X-ray tests, if required)
At this stage, any green sand casting defects—such as porosity, inclusions, or cold shuts—are identified and documented. In most cases, they can be prevented in future cycles by adjusting mold compaction, moisture levels, or pouring speed.
Tools, Equipment, and DIY Kits
Foundry Tools Required for Green Sand Casting
Whether you’re operating a large-scale production line or a small workshop, green sand casting requires specific tools to shape, compact, pour, and finish each casting properly. These tools help ensure consistency, minimize defects, and maintain operator safety.
Here are the most essential tools used in green sand metal casting:
- Flask (Drag & Cope)
A two-part box that holds the sand mold. The drag is the bottom half; the cope is the top. They form the cavity when closed together. - Pattern
A model of the part to be cast. Depending on precision needs, it may be made of wood, plastic, aluminum, or composite materials. - Rammer
Used to compact sand around the pattern inside the flask. This helps achieve a dense mold with proper dimensional accuracy. - Slicks & Trowels
Hand tools for finishing and smoothing the surface of the mold cavity. These help eliminate loose particles and improve surface finish. - Sprue Cutter / Sprue Pin
Used to form the vertical channel (sprue) through which molten metal is poured into the mold. - Vents / Vent Wire
Thin rods used to create air escape routes in the mold. This prevents gas build-up that can lead to casting defects. - Crucible and Furnace
The crucible holds the metal, and the furnace melts it. For aluminum green sand casting, a propane or induction furnace is typically used. - Pouring Ladle
A long-handled vessel used to transfer molten metal safely into the mold cavity. - Protective Equipment
Heat-resistant gloves, goggles, apron, and face shield are essential for safety.
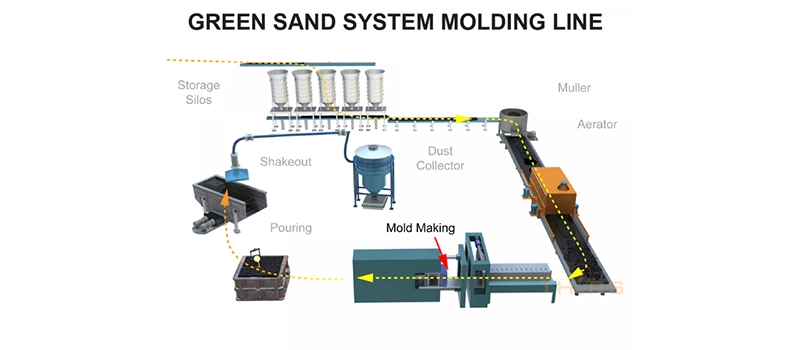
Equipment for Small Workshops vs. Industrial Scale
The core principles of green sand casting remain the same at every scale—but the equipment changes drastically based on production volume, precision requirements, and automation needs.
🔧 For Small Workshops or Hobbyists:
- Manual ramming tools
- Steel or aluminum flasks
- Propane gas furnace for melting aluminum or bronze
- Homemade green casting sand using a standard recipe (silica + bentonite + water)
- Pouring ladles with 1–3 kg capacity
This setup is ideal for DIY green sand for casting, small-batch prototypes, or educational use.
🏭 For Industrial Foundries:
- Automated sand mixers and reclaimers
- CNC-machined pattern sets for repeat accuracy
- High-capacity induction furnaces for iron or steel
- Robotic pouring systems
- On-line sand conditioning and testing systems
At industrial scale, the focus shifts to throughput, repeatability, and casting quality control—especially when producing castings for sectors like agriculture, automotive, or petrochemical valves.
DIY Green Sand: What You Need to Know
Can you make your own green casting sand at home? Absolutely. Many small workshops and educational setups create reliable green sand using simple ingredients. Here’s a basic recipe you can follow:
- 90% silica sand
- 10% bentonite clay
- 3–4% water, added slowly while mixing
Optional: Add 1–2% sea coal or flour to improve collapsibility and surface finish, especially when working with aluminum.
💡 Tip: Use a spray bottle to add water while mixing to prevent over-saturation.
For those experimenting with green sand casting aluminum, this DIY mix is both safe and effective. Always wear protective gear, even at small scale, and never pour metal in enclosed or non-ventilated areas.
Where and How Green Sand Casting Is Used
Industrial Applications of Green Sand Casting
Green sand casting is widely recognized for its ability to produce durable, cost-effective parts across a variety of sectors. Because it accommodates a wide range of part sizes, complexities, and metals, it remains the preferred casting method for many industrial applications.
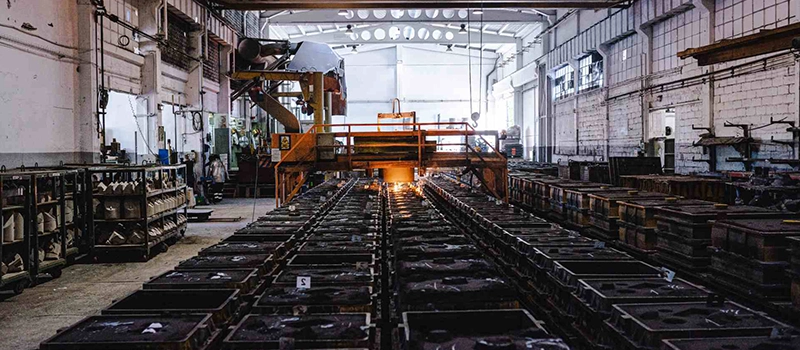
🚜 Agriculture
From tractor brackets to irrigation components, green sand castings offer rugged, corrosion-resistant solutions for demanding agricultural environments. Manufacturers choose this process due to its:
- Fast production cycles for seasonal demand
- Excellent dimensional consistency
- Affordable tooling for complex components
🚗 Automotive
In the automotive sector, green sand iron castings are used extensively for:
- Engine blocks and cylinder heads
- Brake drums and disc housings
- Suspension brackets and frames
OEMs and Tier 1 suppliers rely on this method because of its scalability, lower per-unit cost, and compatibility with ferrous and non-ferrous alloys.
🏗️ Construction & Infrastructure
Green sand casting is ideal for:
- Pipe fittings
- Structural supports
- Joint couplers
- Manhole covers
Its ability to produce heavy-duty, geometrically complex parts in high volume makes it indispensable for infrastructure development projects.
⚙️ Valves & Pumps
Green sand metal casting is commonly used to manufacture:
- Valve bodies
- Impellers
- Pump housings
These components must withstand pressure, temperature fluctuations, and fluid contact—green sand provides the durability and casting accuracy required for such performance-critical applications.
Material-Specific Use Cases
Different industries require different metals, and green sand casting supports a wide range of alloys. Here’s how it’s applied by material:
🟠 Aluminum Green Sand Castings
Lightweight and corrosion-resistant, green sand casting aluminum parts are used for:
- Gear housings
- Pump brackets
- Electrical enclosures
Aluminum castings are often chosen for transportation and HVAC industries where weight reduction is critical.
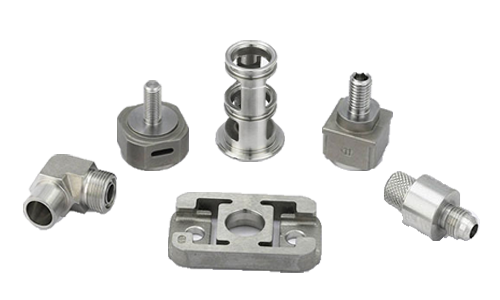
Get a quote now!
⚫ Green Sand Iron Castings
Ductile and gray iron are commonly cast using green sand for:
- Engine components
- Heavy-duty brackets
- Pipe and sewer fittings
Iron provides excellent wear resistance and strength, especially for high-load mechanical systems.
⚙️ Other Non-Ferrous Alloys
Bronze and brass can also be poured into green sand molds—particularly for decorative, marine, or precision applications that require resistance to corrosion and salt exposure.
The ability to adjust the sand mix—grain size, moisture level, additives—allows foundries to optimize for metal-specific shrinkage, flow characteristics, and cooling times.
Why Industries Still Rely on Green Sand Casting
Even with the rise of high-tech casting techniques, industries across the globe continue to choose green sand casting because it offers:
- Low setup cost for new parts
- Flexible batch sizes, from prototypes to mass production
- Ease of customization for metal types and mold configurations
- Faster lead times without compromising performance
- Sustainable material usage aligned with modern compliance standards
This process has proven especially valuable in emerging markets and export-focused factories, where budget control and turnaround speed are essential.
Green Sand vs Other Casting Methods
Green Sand vs Dry Sand Casting
While these two methods sound similar, there’s a big difference between green sand casting and dry sand casting.
- Green sand molds are used in their moist, “green” state.
- Dry sand molds are baked or cured in an oven before pouring.
✅ Advantages of Green Sand:
- Faster mold preparation
- Lower energy consumption
- Reusable sand with simple conditioning
- Ideal for short- to mid-volume production
❌ Limitations vs Dry Sand:
- Slightly rougher surface finish
- Less suited for extremely tight tolerances
Dry sand casting is preferred when moisture could cause steam-related defects in complex castings. However, it comes at the cost of longer cycle times and higher mold preparation energy—something green sand avoids entirely.
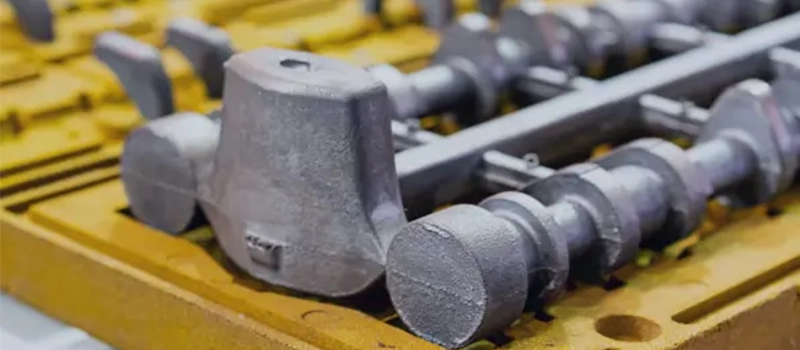
Green Sand vs Investment Casting
Investment casting, also called “lost wax casting,” creates molds by forming wax patterns, dipping them in ceramic slurry, and then melting out the wax to leave a cavity.
✅ Investment Casting Offers:
- Excellent surface finish
- Precise detail and thin walls
- Ideal for complex or ornamental shapes
❌ But Compared to Green Sand:
- Much higher tooling and material costs
- Long lead times (due to mold drying and burnout)
- Not reusable—ceramic shells are single-use only
For cost-sensitive or large-volume industrial production, green sand casting outperforms investment casting in:
- Affordability
- Speed
- Scalability
- Environmental impact (due to sand reuse)
Green Sand vs Die Casting
Die casting involves injecting molten metal into steel molds under high pressure. It’s commonly used for mass production of aluminum or zinc parts in consumer electronics, automotive, and appliance industries.
✅ Die Casting Benefits:
- High dimensional accuracy
- Smooth surface finish
- Fast production once tooling is built
❌ But…
- Very high initial tooling cost
- Only suitable for non-ferrous metals
- Less flexible for design changes
- Not eco-friendly (mold life limited, high energy demand)
Green sand casting, by contrast, is ideal when:
- You need a mix of ferrous and non-ferrous metals
- You’re casting larger or more complex parts
- You want to avoid excessive capital investment
For industrial buyers in agriculture, automotive, or construction, green sand molds allow easier design modifications and faster turnaround without the steep upfront investment of die casting.
Need Help? We’re Here for You!
Choosing the Right Casting Method for Your Needs
So—why is green sand casting still the smart choice?
Because it provides the best balance of:
- Initial cost
- Lead time
- Volume flexibility
- Eco-sustainability
- Wide metal compatibility
It’s particularly well-suited for industrial customers looking to optimize for speed and scalability without sacrificing quality.
If your priorities include:
- Competitive pricing
- Low environmental impact
- Reliable production with material versatility
Then green sand casting is likely your best bet.
How to Get Clean, Accurate Castings Every Time
Best Practices for Mold Strength and Surface Quality
The quality of a green sand casting depends heavily on how well the mold is prepared. A strong, well-compacted mold ensures:
- Accurate dimensional reproduction
- Smooth surface finish
- Reduced chance of casting defects like warping or shrinkage
Here are some best practices to follow:
- Uniform Ramming Pressure: Inconsistent pressure creates weak spots. Manual or pneumatic ramming must be evenly applied around the pattern.
- Correct Sand Moisture: Ideal moisture content is typically 3–4%. Too dry and the sand crumbles; too wet and the mold collapses or creates gas pockets.
- Proper Sand Grain Size: Fine grains improve surface finish but reduce permeability. Coarser grains enhance airflow but leave a rougher finish. Balance is key.
Using a calibrated sand testing kit helps monitor:
- Moisture content
- Clay activation levels
- Compression strength
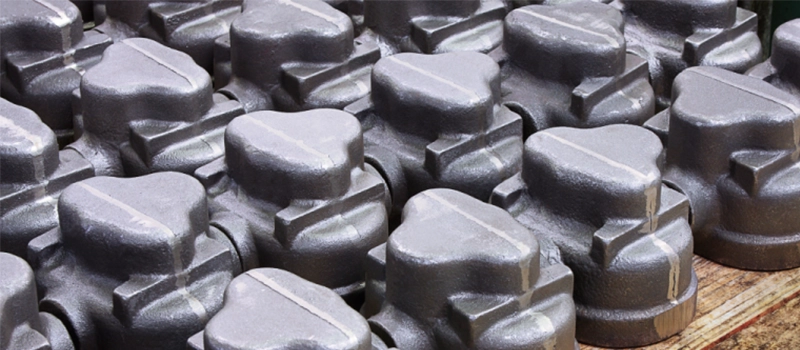
Moisture Control and Sand Conditioning
Moisture is one of the most critical yet overlooked variables in green sand metal casting. Improper control leads to problems like:
- Blowholes from steam generation
- Mold washout during pouring
- Weak mold strength or poor finish
Foundries often implement automatic moisture control systems to continuously measure water content and inject precise amounts during mixing.
Key moisture control tips:
- Use spray atomizers instead of direct pouring
- Store mixed sand in sealed containers to prevent evaporation
- Avoid overworking old sand that’s been recycled too many times
Well-conditioned green sand delivers uniform mold performance, which is essential when casting high-demand parts like pump bodies or automotive brackets.
Common Defects and How to Avoid Them
Even in optimized systems, green sand casting defects can occur. Here’s a breakdown of the most frequent ones and how to avoid them:
🔴 Porosity
Tiny holes or air pockets inside the casting.
Cause: Trapped gases due to poor venting or high moisture.
Solution: Use more vent wires and monitor sand moisture precisely.
🔴 Misruns
Metal fails to fill the mold completely.
Cause: Low metal pouring temperature or thin mold sections.
Solution: Preheat molds or increase gating system cross-section.
🔴 Rough Surface Finish
Granular or pitted casting surfaces.
Cause: Coarse sand grains, low mold compaction, or excessive additives.
Solution: Use finer sand, improve ramming, and test binder ratios.
🔴 Metal Penetration
Molten metal seeps into mold sand, leaving a rough shell.
Cause: Low sand density or weak binder activity.
Solution: Increase ramming pressure and recheck bentonite/clay activation.
Improving Surface Finish Without Raising Costs
If your buyers or customers demand smoother surfaces, but you want to avoid switching to more expensive processes like investment casting, consider these green sand upgrades:
- Add graphite powder or sea coal as parting agents
- Use finer sand grains in contact areas (facing sand)
- Apply a ceramic mold wash to improve finish without affecting permeability
These simple changes can dramatically enhance green sand casting surface finish, particularly in aluminum and decorative bronze castings—while keeping your costs under control.
Need Help? We’re Here for You!
What to Consider When Choosing Green Sand Casting Services
Why Choosing the Right Supplier Is Critical
Selecting the right green sand casting service provider is not just about finding the lowest price—it’s about ensuring quality, consistency, and accountability. A misjudged supplier can lead to casting defects, production delays, and unexpected costs. That’s why it’s essential to evaluate each foundry’s technical abilities, communication standards, and export capabilities before committing to a project.
Key Factors to Evaluate When Choosing a Supplier
🔧 1. Production Capability and Scalability
Can the supplier handle your required volume—from small-batch prototyping to mass production? Do they have dedicated green sand casting lines with repeatable processes? It’s important that they can scale with your business, rather than become a bottleneck when demand increases.
🧪 2. Material Handling and Sand Expertise
A professional casting provider should know how to adjust green sand composition based on metal type, part size, and finish requirements. Their ability to manage various alloys—like iron and aluminum—demonstrates technical maturity.
✅ 3. Quality Assurance Systems
Quality control is non-negotiable. Look for internal protocols like dimensional inspection, mold integrity checks, and material traceability. Suppliers should provide inspection reports and have procedures in place to address any production errors.
🎯 4. Surface Finish and Defect Management
Can the supplier consistently deliver clean castings? Ask how they manage common green sand casting defects, such as porosity or misruns. Their ability to produce tight tolerances and smooth surfaces reduces the need for excessive post-processing.
📂 5. Engineering and Design Support
Is there a qualified team to review your drawings and provide technical feedback? Effective collaboration during the design stage often determines the casting’s final performance and cost-efficiency.
🌍 6. Lead Time and Export Logistics
An ideal supplier not only meets your deadlines but also understands global shipping and documentation. If you’re exporting, check whether they offer help with FOB/CIF, customs clearance, and packaging optimization.
Why Dalian ZhongSheng Metal Products Is the Right Choice
At Dalian ZhongSheng Metal Products, we meet and exceed every criterion listed above. With decades of experience and continuous investment in green sand casting technology, our factory has grown into a reliable supplier trusted by industrial buyers across North America, Europe, Japan, and South Korea.
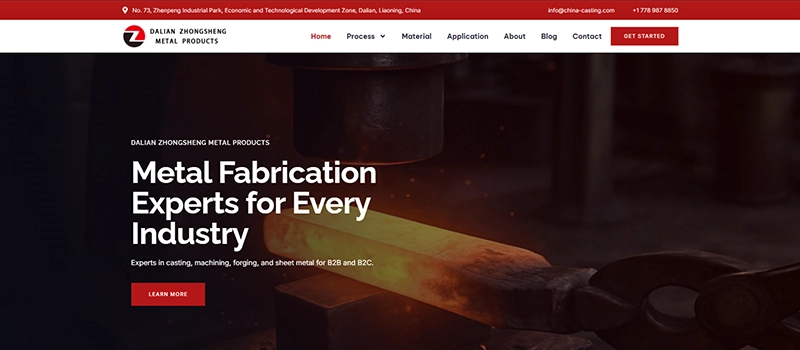
- Flexible batch sizes and fast tooling turnaround
- Sand customization for both aluminum and iron castings
- Strict quality control backed by CE and GPSR EU compliance
- Professional drawing evaluation and 1-on-1 engineering support
- Support for global trade terms (FOB, CIF, DDP) with reliable shipping coordination
If you’re looking for a casting supplier that understands your expectations, communicates clearly, and delivers on time, we’re ready to support your business. Let’s build something strong—together.
What’s Next for Green Sand Casting?
Sustainability Is Driving the Next Era
As global industries shift toward net-zero goals, the casting industry is under pressure to reduce emissions, waste, and energy consumption. Fortunately, green sand casting is already positioned as one of the most eco-friendly metalworking methods—but there’s still room to improve.
Foundries are now investing in:
- Energy-efficient furnaces (e.g., induction heating)
- Sand reclamation systems that reduce waste by over 90%
- Closed-loop water recycling during mold preparation
- Environmentally friendly additives that eliminate hazardous emissions
These enhancements align with international environmental standards such as ISO 14001 and growing corporate ESG requirements. As clients worldwide push for cleaner supply chains, green sand casting’s recyclability and lower carbon footprint give it a strong competitive edge.
Automation and AI in Foundry Operations
The rise of Industry 4.0 is transforming how green sand casting is managed on the shop floor. Foundries are now integrating smart automation systems to enhance productivity and casting quality.
Here’s what the modern green sand foundry looks like:
- Automated mold compaction machines that deliver consistent pressure
- Sensor-driven sand mixers that monitor moisture and binder ratios in real time
- Digital pouring control systems to manage temperature and flow rate
- AI-powered defect detection using real-time camera inspection and pattern recognition
These advancements reduce human error, improve repeatability, and minimize downtime. They also help new operators get up to speed faster with fewer training hours required.
For buyers, this means:
- More consistent product quality
- Shorter lead times
- Lower defect rates
- Real-time production visibility (if integrated with ERP or MES systems)
Global Trends Favoring Green Sand Casting
Several global manufacturing trends are increasing the demand for green sand casting:
🌎 Reshoring and Diversification of Supply Chains
Buyers are looking for regional partners to reduce risk and lead times. Foundries that offer green sand casting with rapid response capability are becoming strategic assets.
📈 Rapid Prototyping for Industrial Components
With the help of 3D-printed patterns, green sand casting is being adopted for prototype runs—bridging the gap between design and full production faster than traditional methods.
💡 Custom Alloy Development
Foundries are working closer with buyers to develop special alloy castings tailored to specific load, corrosion, or thermal requirements—all while using green sand molding systems for cost efficiency.
A Future Built on Flexibility and Efficiency
Green sand casting isn’t a thing of the past—it’s a platform for the future. Its ability to evolve with new materials, automation, and sustainability practices makes it one of the most resilient and versatile manufacturing processes available today.
As global standards rise, buyers will increasingly demand casting solutions that are:
- Technically advanced
- Cost-efficient
- Environmentally responsible
Foundries that embrace this direction—like ours—will continue to lead the way in quality, speed, and value.
Conclusion
Green sand casting continues to prove itself as a powerful solution for manufacturers seeking reliability, affordability, and sustainability. With advancements in automation, environmental compliance, and material flexibility, this timeless method is more relevant than ever. For businesses that value quality without compromise, green sand casting remains the smart, future-ready choice.