Are you struggling with inconsistent part quality? Is your production timeline always under pressure from delayed deliveries? Are rising machining costs and poor tolerance control cutting into your profits? Do you find it difficult to source CNC machining services that meet both quality and price expectations?
CNC machining services solve these exact challenges by delivering precision, consistency, and cost-efficiency—key elements in today’s highly competitive industrial landscape. Whether you operate in automotive, agriculture, petrochemical, valve, or construction sectors, understanding CNC machining is no longer optional—it’s a necessity. These services help businesses like yours transform complex designs into high-precision parts with tight tolerances, fast turnaround times, and minimal waste.
In this comprehensive guide, we’ll walk you through every aspect of CNC machining services. From machine types and material selection to supplier evaluation and cost optimization, you’ll gain practical insights to make informed decisions. We’ll also explore how precision CNC machining can reduce downtime, elevate product quality, and drive profitability in your operations. Join me as we explore the power of CNC machining and how it can position your business for long-term success in today’s fast-evolving manufacturing world.
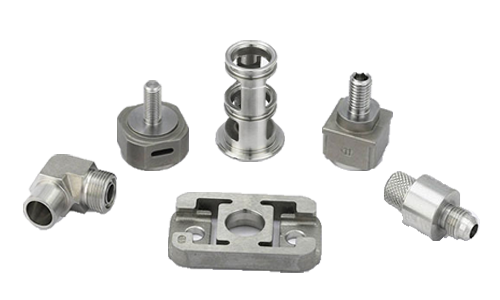
Get a quote now!
What Are CNC Machining Services
Understanding the Foundation of Precision Manufacturing
CNC machining services refer to the process of using Computer Numerical Control (CNC) technology to manufacture high-precision parts and components. This automated process controls machinery—such as mills, lathes, grinders, and routers—through computer-generated code to shape materials like metal, plastic, or composites.
At its core, CNC machining replaces manual control with digital instructions. A pre-programmed file tells the machine how to move, what paths to follow, what tools to use, and how fast to operate. This results in repeatable, ultra-accurate production with minimal human error.
There are several types of CNC machining processes:
- CNC milling for cutting and drilling;
- CNC turning for cylindrical parts;
- CNC drilling for creating precise holes;
- 5-axis CNC machining for complex geometries.
Each method plays a unique role depending on the shape, material, and specifications of the final product.
In today’s fast-paced manufacturing world, CNC machining services are essential for industries requiring tight tolerances, consistent quality, and high-volume production. From aerospace to automotive, construction to petrochemical, this technology supports the efficient creation of both simple and highly intricate parts.
Because the entire machining process is automated, CNC services also offer cost advantages over manual machining—especially for large production runs or complex components. The digital nature of CNC allows for quick modifications, better quality control, and faster turnaround times, which are crucial for modern industrial operations.
Put simply, CNC machining services are the backbone of modern manufacturing. Whether you’re producing a single prototype or thousands of units, CNC technology ensures every part meets exact design specifications, every time.
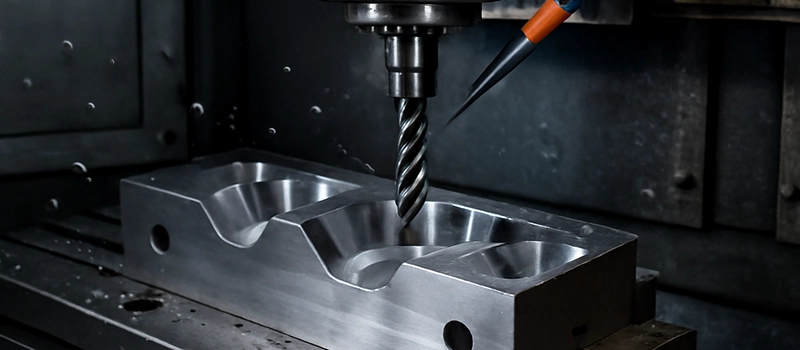
Why CNC Machining Services Matter in Modern Manufacturing
Consistent Precision in Every Production Run
In a world where tolerances are tight and margins even tighter, CNC machining services offer unmatched precision. Once programmed, CNC machines replicate parts with extreme accuracy—down to fractions of a millimeter. This consistency is critical in industries like automotive, valve, and construction, where one defective component can lead to costly failures or safety issues.
By eliminating human error and automating tool movement, CNC ensures every part is manufactured to exact specifications, every time. Whether you’re producing custom prototypes or large-scale components, CNC guarantees reliable results across the board.
Flexibility and Speed in Adapting to Design Changes
One of the key advantages of CNC machining services is adaptability. When product requirements evolve—such as material changes, dimensional updates, or geometry revisions—the digital nature of CNC programming allows for rapid file modifications without changing the physical setup.
This agility is especially beneficial for agriculture and petrochemical industries, where component redesigns may occur due to environmental conditions or regulatory changes. Faster iteration means faster time to market and greater responsiveness to customer needs.
Need Help? We’re Here for You!
Scalable Production That Lowers Long-Term Costs
Unlike manual machining, which is labor-intensive and difficult to scale, CNC machining services can handle anything from small batch orders to full production runs. Once the setup is done, parts can be produced 24/7 with little supervision—reducing overhead and labor costs dramatically.
This scalability means that companies can take on more projects, expand their offerings, or respond to demand surges without losing control over quality or lead times. For businesses trying to grow while keeping costs predictable, CNC machining provides the ideal solution.
Key CNC Machining Processes Explained
CNC Milling: Cutting with Precision and Versatility
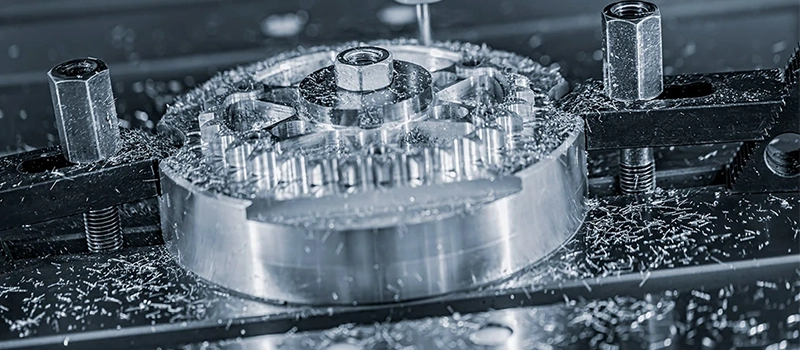
CNC milling is one of the most common and versatile machining methods used in modern manufacturing. It involves using rotary cutting tools to remove material from a workpiece, typically on a 3-axis or 5-axis CNC machining center. The machine moves the workpiece and/or the cutting tool along multiple axes to achieve complex shapes with high accuracy.
This process is ideal for parts that require pockets, slots, or intricate contours. Industries like automotive and construction rely heavily on CNC milling for both prototyping and full-scale production. Advanced 5-axis CNC machining services are particularly useful when dealing with curved surfaces or multi-faceted designs.
CNC Turning: Perfect for Cylindrical Components
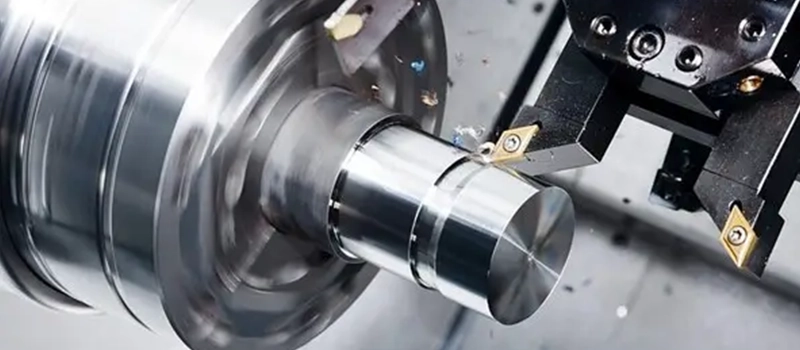
CNC turning, also known as CNC lathing, is designed to produce round or tubular components. The material rotates while a stationary cutting tool shapes it into the desired form. It’s perfect for parts like bushings, valve spools, and connector pins.
CNC lathe machining is faster and more cost-efficient for high-volume production of cylindrical parts. With tight control over tool position, precision CNC machining delivers smooth finishes and tight tolerances critical in valve and petrochemical applications.
CNC Drilling, Boring, and Tapping: Creating Perfect Holes
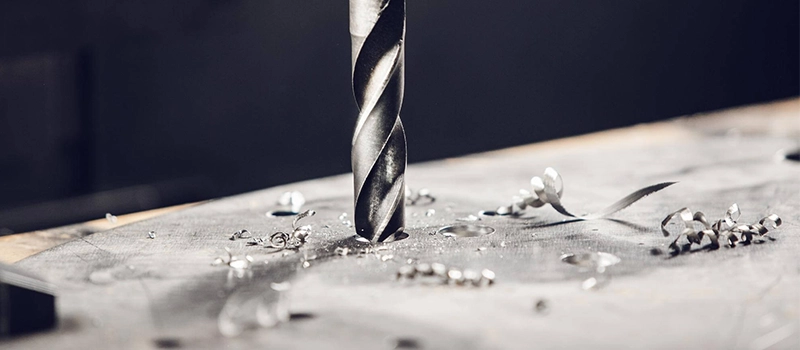
While basic drilling might sound simple, CNC drilling ensures that holes are made with consistent depth, diameter, and placement. This is crucial in components like engine blocks or flange plates, where even a tiny misalignment can ruin the functionality.
In addition, boring is used to refine existing holes with greater accuracy, and tapping creates internal threads—both are vital in assembly-based industries like automotive and industrial machinery.
Electrical Discharge Machining (EDM): Precision Without Contact
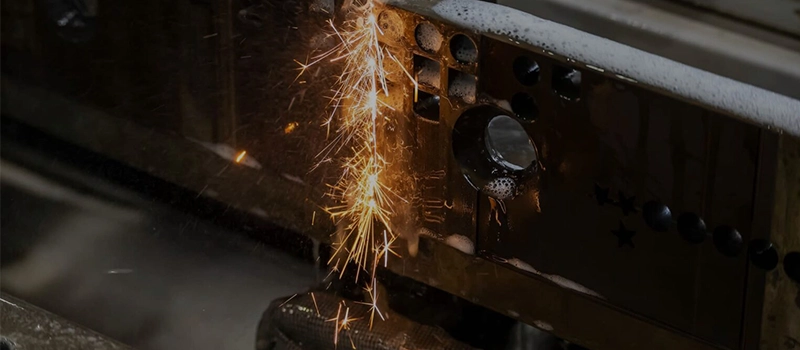
EDM is a specialized process used when traditional machining can’t achieve the desired results, especially with hard metals or intricate geometries. It uses electrical discharges to erode the material and is common in toolmaking, mold manufacturing, and tight-tolerance component creation.
Though slower than other methods, EDM excels in producing complex cavities or working with hardened alloys where regular cutting tools would wear out quickly.
Multi-Axis CNC Machining: Unlocking Complex Part Geometry
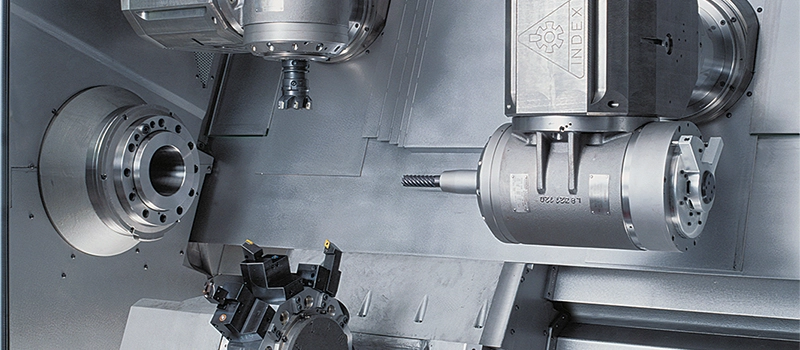
The evolution of 3-axis, 4-axis, and 5-axis CNC machining has opened doors to more complex part production. In multi-axis CNC machining, the cutting tool or workpiece can rotate in additional directions, reducing the need for multiple setups and enhancing precision.
5-axis CNC machining services are often used in aerospace, medical, and precision engineering, where part geometry is highly complex and margins for error are razor-thin.
What Materials Can Be Used in CNC Machining
Choosing the Right Material for Your CNC Project
Material selection is one of the most critical decisions when using CNC machining services. The material you choose will affect everything—from machining speed and surface finish to strength, corrosion resistance, and overall cost. With CNC, you can work with a wide variety of metals, plastics, and even composites, depending on the application.
The key is to match the material’s physical properties with the performance demands of the final part. For instance, a valve body in the petrochemical industry will require different properties than a lightweight structural bracket for agricultural equipment.
Popular Metals for CNC Machining
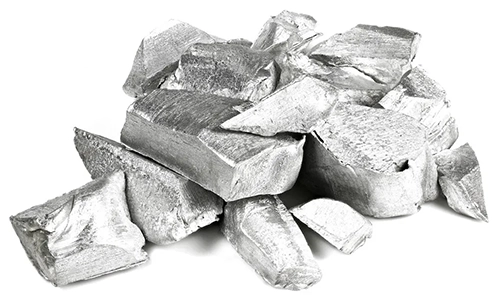
Aluminum
Aluminum CNC machining is popular because it’s lightweight, corrosion-resistant, and easy to work with. Grades like 6061-T6 aluminum are widely used in automotive, aerospace, and construction components.
Steel and Stainless Steel
Steel is chosen for its strength and wear resistance. Stainless steel CNC machining is especially common in environments requiring corrosion resistance, such as petrochemical and valve systems. Machining stainless steel can be more difficult, but it’s essential for critical parts under pressure or exposure to harsh chemicals.
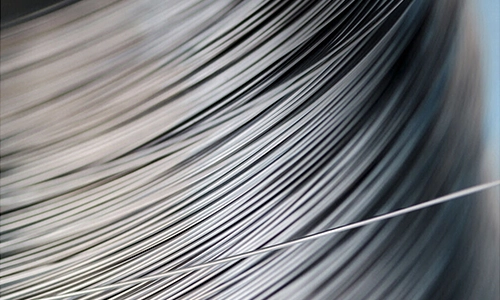
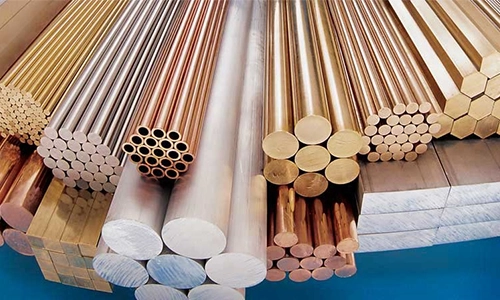
Brass and Bronze
CNC machining bronze is ideal for valve bodies and fittings that require low friction and anti-corrosive properties. Brass is easier to machine and is commonly used in fittings, gears, and bushings.
Titanium
Titanium CNC machining is more specialized and used in aerospace, medical, and marine applications. It’s expensive but offers unmatched strength-to-weight ratio and corrosion resistance.
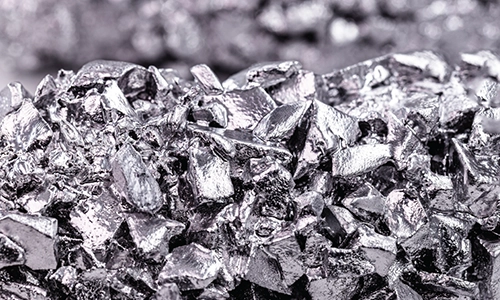
Engineering Plastics and Composites
Although metals dominate the CNC world, engineering plastics like POM (Delrin), Nylon, and PTFE (Teflon) are also frequently machined. These are ideal for non-conductive, lightweight, or chemical-resistant components. While they can’t match metals in structural strength, they excel in electrical insulation, wear resistance, and chemical compatibility.
Material Considerations for CNC Machining
When selecting materials for CNC machining services, consider the following:
- Machinability: How easily the material can be cut without excessive wear on tools.
- Mechanical Properties: Strength, ductility, hardness, and fatigue resistance.
- Thermal Stability: Will the part endure high heat or temperature cycling?
- Corrosion Resistance: Is the part exposed to moisture, chemicals, or saltwater?
- Cost and Availability: Balance performance with budget constraints.
Different materials also have different requirements for tooling, cutting speeds, and coolants, all of which can affect CNC machining cost and turnaround time.Choosing the right material is more than just a technical step—it’s a strategic decision that affects the success and longevity of your product.
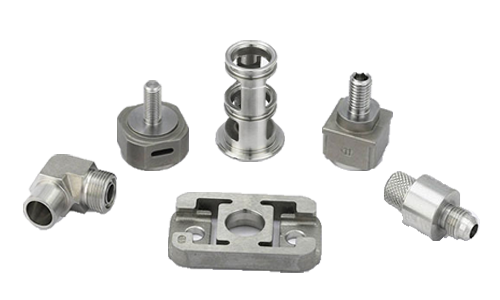
Get a quote now!
Which Industries Use CNC Machining Services and Why?
Meeting the Demands of Modern Industrial Applications
CNC machining services are critical to industries that demand high precision, tight tolerances, and scalable production. From heavy machinery to high-tech devices, the flexibility and reliability of CNC make it the go-to manufacturing solution for countless applications.
Whether you’re producing parts for rugged outdoor equipment or mission-critical components for petrochemical systems, CNC machining offers the accuracy, speed, and repeatability required to meet modern industrial standards.
Automotive: Precision Parts for Performance and Safety
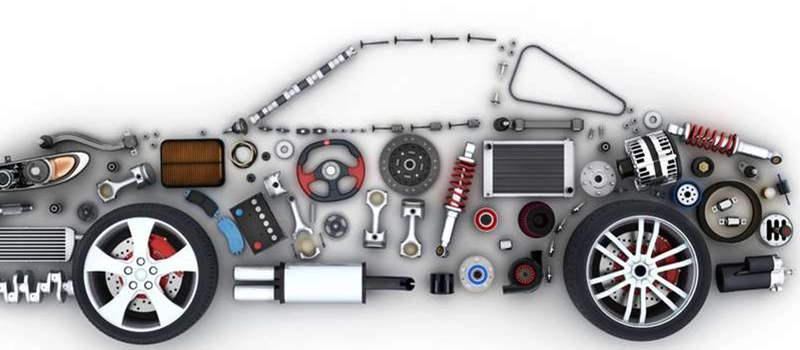
The automotive industry relies heavily on CNC machining services for everything from engine components to transmission housings and suspension brackets. These parts must meet strict performance specifications and undergo rigorous quality control.
CNC allows for rapid prototyping and mass production of customized automotive parts, ensuring vehicles are not only functional but also safe and efficient. Because the industry deals with both metal and plastic components, CNC’s versatility in material handling is a major advantage.
Agriculture: Durable Components for Tough Environments
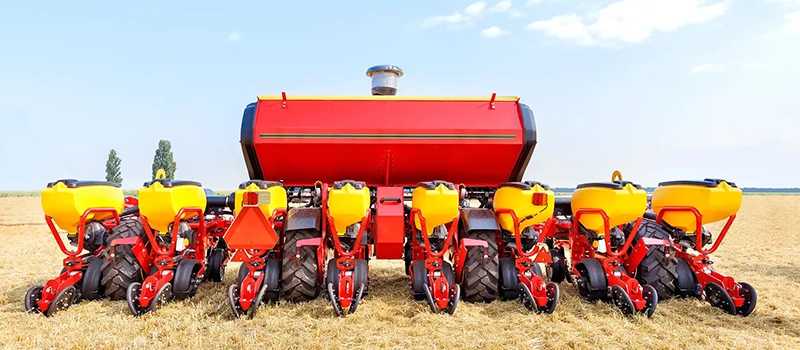
Agricultural machinery operates under extreme conditions—mud, dust, vibration, and impact. CNC machining ensures that critical parts like blade holders, shaft brackets, and hydraulic couplings are made from materials that withstand wear and tear.
CNC machining services make it possible to produce rugged, corrosion-resistant components quickly and affordably, helping manufacturers maintain uptime and equipment reliability in the field.
Construction and Heavy Equipment: Strength and Scale
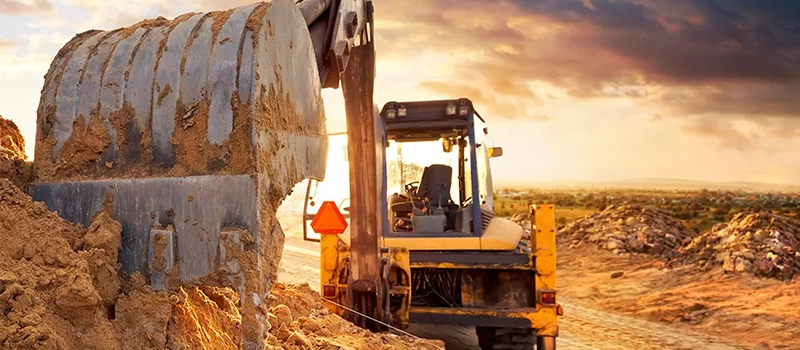
In the construction industry, CNC is used to fabricate parts for loaders, cranes, and excavators. These machines require high-strength steel parts, often in medium to large batch sizes.
CNC machining services deliver the precision needed for components like axle supports, gear housings, and chassis connectors, ensuring structural integrity and long service life.
Valve and Petrochemical: Tolerance and Corrosion Resistance
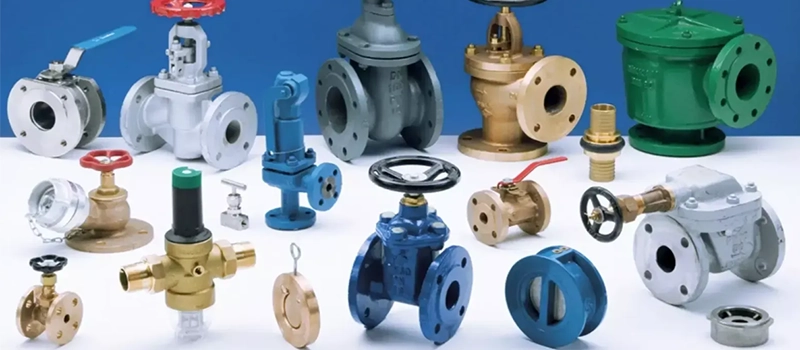
Valves and fittings used in petrochemical plants must operate under high pressures, corrosive fluids, and temperature extremes. CNC allows for the production of close-tolerance parts from materials like stainless steel, bronze, and titanium.
The valve industry especially benefits from CNC machining services that offer tight dimensional control and traceability. With CNC, complex internal geometries and sealing surfaces can be machined to exact specifications.
Aerospace and Medical: Zero Margin for Error
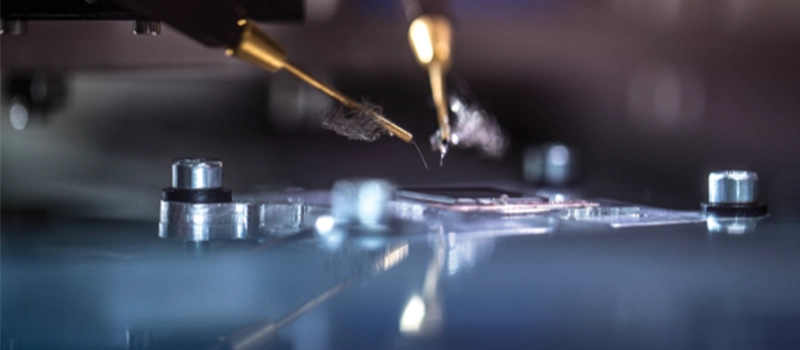
Although your business may not directly target aerospace or medical sectors, it’s important to note that precision CNC machining is vital here. These industries demand ultra-tight tolerances, certified materials, and flawless finishes.
CNC machining’s ability to meet these standards showcases its capability to support high-end industrial applications—further reinforcing its value across all sectors.
CNC machining services adapt to the specific demands of each industry. Whether you’re after durability, speed, precision, or scalability, CNC provides a tailored solution that helps businesses meet strict technical and commercial requirements.
What Are the Benefits of CNC Machining Services?
Precision and Repeatability
One of the most significant advantages of CNC machining services is their ability to deliver highly accurate, repeatable results. Once a digital design is programmed, the machine can produce part after part with micron-level precision—no matter the volume. This is crucial in industries like automotive, petrochemical, and construction, where a tiny deviation can lead to costly failures or safety issues.
By eliminating human error, CNC machining ensures that each component meets its exact design specifications, maintaining tight tolerances across every production run.
Flexibility Across Materials and Designs
CNC machining services are incredibly flexible in both materials and geometries. Whether you’re working with 6061-T6 aluminum, stainless steel, bronze, or even titanium, CNC machines can handle the job. And whether you need simple shapes or multi-axis precision machining, the process adapts easily to changing project requirements.
This versatility allows manufacturers to prototype quickly, test new designs, or scale up to mass production without redesigning the tooling or compromising on quality.
Efficiency and Speed
Thanks to automation and computer control, CNC machining dramatically reduces the time needed to produce complex parts. There’s no need for manual repositioning or tool changes—everything is programmed and executed with speed and efficiency.
This not only leads to faster turnaround times but also supports 24/7 production, enabling companies to meet tight deadlines without sacrificing quality.
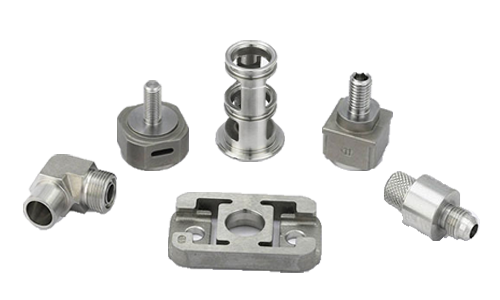
Get a quote now!
Lower Operational Costs
While CNC machines represent a higher initial investment, they significantly reduce labor, waste, and rework in the long run. This results in lower overall production costs, particularly for high-volume orders. You also avoid the costs associated with quality failures, which can be substantial in industrial environments.
For businesses operating on tight margins, especially in developing manufacturing markets, CNC machining offers cost efficiency without sacrificing quality.
Scalability and Consistency
Once a design is finalized, it can be used to create one part—or a million—with identical quality. This scalability makes CNC ideal for both small-batch prototyping and large-scale production, providing flexibility as your needs evolve.
Whether you’re a startup testing a new product or a major manufacturer fulfilling large orders, CNC machining services ensure your output remains consistent and reliable.
Enhanced Quality Control
Because CNC machining operates based on exact digital instructions, it’s easier to implement automated quality control measures. Inspection systems can verify dimensions during or immediately after machining, ensuring compliance with strict industrial standards.
This means fewer defects, higher customer satisfaction, and a stronger reputation in your market.
How Much Does CNC Machining Cost?
Understanding the Cost Structure of CNC Machining Services
When customers consider CNC machining services, one of the first questions is:
“How much does CNC machining cost?”
The answer isn’t always simple—it depends on several variables. CNC machining pricing is typically calculated based on machine time, material costs, part complexity, volume, and additional services such as finishing or inspection.
Knowing what affects these costs can help you make smarter sourcing decisions and avoid hidden expenses.
Key Factors That Influence CNC Machining Costs
- Material Selection
Materials like aluminum and steel are more affordable and widely available, while specialty metals such as titanium or bronze are more expensive to procure and harder to machine. More difficult materials also require more tool changes and slower cutting speeds. - Part Complexity
Intricate designs, tight tolerances, and multi-surface geometries (especially on 5-axis CNC machining centers) take longer to machine and require more programming time. Simple shapes cost less; complexity adds up. - Machining Time and Setup
Machine time is a major cost driver. CNC machines are billed per hour, ranging from $30 to over $100 USD per hour, depending on the machine type and precision level. The setup time is also factored in—especially for low-volume or prototype orders. - Quantity and Batch Size
High-volume orders benefit from economies of scale. The more units you produce, the lower the cost per piece. Conversely, small batches may include higher setup and programming costs per unit. - Tolerances and Surface Finish
Tighter tolerances and better surface finishes require additional machining steps, slower feed rates, or secondary finishing, all of which increase cost. - Post-Processing Requirements
Services like anodizing, coating, engraving, or heat treating are often priced separately. If your part needs extra durability, corrosion resistance, or cosmetic improvements, expect those costs to be added. - Shipping and Logistics
International shipping costs, import duties, and packaging add another layer of cost—especially if you’re sourcing CNC machining services from China or other countries.
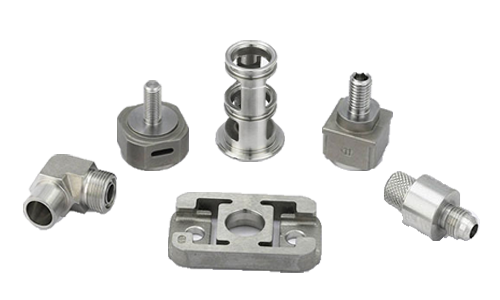
Get a quote now!
How to Estimate CNC Machining Cost More Accurately
To calculate costs with more confidence, you’ll need to provide:
- A detailed CAD drawing with dimensions and tolerances
- The desired material
- The required surface finish
- Your order quantity
- Preferred lead time
Many CNC service providers offer instant online quotes—especially for standard materials and part shapes. However, for more complex or custom jobs, manual evaluation is often required to ensure accurate pricing.
Tips to Reduce Your CNC Machining Costs
- Use standard tolerances unless tighter ones are essential
- Simplify your part design to reduce machine time
- Choose materials that balance performance and cost
- Order in bulk when possible to lower per-unit cost
- Work with suppliers that offer in-house services to avoid third-party markups
How to Choose the Right CNC Machining Services Provider
What to Look for in a Reliable CNC Partner
Choosing the right provider for CNC machining services is critical to your project’s success. The quality of the parts you receive, the accuracy of delivery timelines, and the overall production cost are all affected by your supplier’s capability and reliability.
But with so many vendors available—especially online—how do you find the one that truly meets your needs?
Key Factors to Evaluate
- Production Capabilities
Can the provider handle both prototypes and large-scale production? Do they offer a variety of machining services like CNC milling, turning, and multi-axis machining? A capable partner should have a diverse, modern machine shop and technical expertise in handling complex projects. - Material Expertise
Look for a manufacturer experienced with your required materials—whether it’s 6061-T6 aluminum, stainless steel, bronze, or titanium. Material behavior during machining can significantly impact both part quality and cost. - Certifications and Quality Control
Are they certified? What inspection processes do they use? Reputable providers should follow international quality standards, offer detailed inspection reports, and implement rigorous in-process QC procedures. - Transparency and Communication
A good supplier provides clear quotations, responsive support, and keeps you updated on production and logistics. Communication gaps often lead to mistakes, delays, and cost overruns. - Shipping and After-Sales Support
Can they ship internationally with efficient timelines? What happens if there’s a quality issue post-delivery? Your supplier should have reliable logistics experience and offer after-sales service guarantees.
Why We’re Trusted by Global Buyers
At Dalian ZhongSheng Metal Products, we provide one-stop CNC machining services tailored for industrial clients worldwide. With over 30 years of manufacturing experience, our facility in Dalian, China, covers everything from casting and forging to precision CNC machining under one roof.
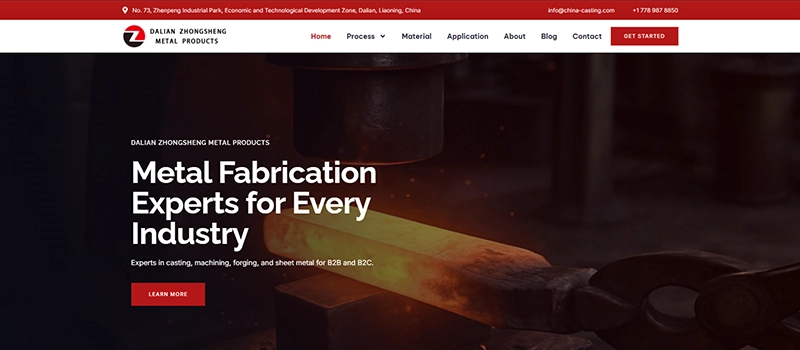
Our workshop includes:
- CNC vertical and horizontal machining centers
- 3-axis and 5-axis CNC equipment
- Full in-house inspection systems
- EU representative certification for export compliance
We support industries such as automotive, agriculture, petrochemical, and construction, and deliver parts with tight tolerances, fast lead times, and competitive pricing.
From initial drawings to final shipment, we’re committed to providing high-quality, custom CNC machining solutions that meet your exact requirements.
What’s Next: Trends and Innovations in CNC Machining
Smarter CNC Machining Through Automation
The world of CNC machining services is evolving fast. As global industries demand greater precision, faster turnaround, and smarter production systems, automation and AI integration are transforming how CNC machines operate.
Advanced CNC control software now optimizes tool paths in real time, reduces material waste, and predicts maintenance before breakdowns occur. This not only improves productivity but also extends the lifespan of expensive machining equipment.
Multi-Axis Machining for Complex Geometry
While 3-axis machining has long been standard, today’s projects often require 4-axis and 5-axis CNC machining services. These systems allow for more complex geometries, fewer setups, and better surface finishes—all with shorter cycle times.
As product designs become more intricate, multi-axis capability is increasingly essential for industries like aerospace, medical, and even automotive where efficiency and accuracy go hand in hand.
CNC Machining + Additive Manufacturing (Hybrid Processes)
Another emerging trend is the integration of CNC machining with additive manufacturing (such as 3D printing). In this hybrid model, parts are first 3D printed for speed and flexibility, then finished with CNC machining for accuracy and surface quality.
This opens new possibilities in rapid prototyping, custom tooling, and even low-volume production where cost and time are critical.
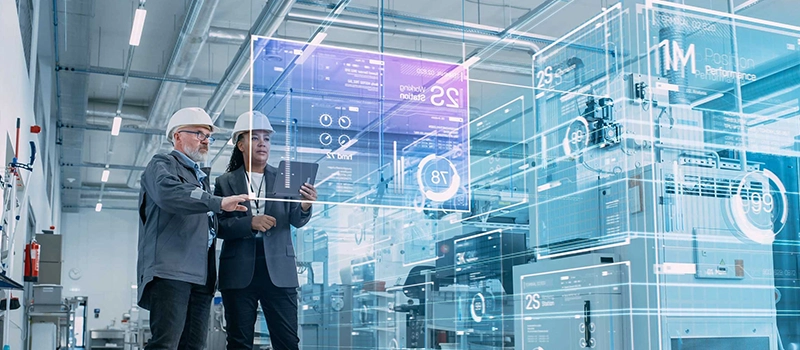
Sustainable CNC Machining Services
Environmental concerns are driving demand for eco-friendly CNC machining practices. This includes using coolant recycling systems, energy-efficient machine tools, and selecting low-waste materials.
More manufacturers—especially in North America and Europe—are seeking CNC partners who can support sustainable practices while still delivering competitive prices and precision parts.
What It Means for Your Business
As a buyer or engineer, staying informed about these trends helps you select the right machining partner, anticipate technological shifts, and design smarter, more manufacturable products.
The future of CNC machining services isn’t just faster and more automated—it’s smarter, more adaptable, and deeply integrated into the entire product development lifecycle.
Conclusion: Why CNC Machining Is Essential for Your Business Success
CNC machining services are no longer a luxury—they’re a manufacturing essential. Whether you’re producing prototypes, custom parts, or large-scale industrial components, CNC offers the speed, accuracy, and consistency needed to compete in today’s global market.
By understanding the processes, materials, costs, and emerging technologies, you’re better equipped to choose the right service provider and unlock the full potential of precision manufacturing.
Ready to elevate your production quality and efficiency? It starts with CNC.