Facing the choice between carbon steel vs cast iron for your next industrial project? Wondering which one offers better strength for structural parts? Is cast iron more cost-effective in casting? Will carbon steel really hold up better under tension and shock? Confused about which metal machines cleaner, welds easier, or performs more reliably in long-term industrial use? Are you worried that choosing the wrong material could lead to production delays, higher costs, or even customer complaints?
These are the exact concerns many industrial buyers face when comparing carbon steel vs cast iron. Although both materials are staples in fabrication and metalworking, they behave very differently in processing, durability, and performance. One offers flexibility and weldability; the other provides dimensional stability and better wear resistance. And what seems like a small choice at the start of your procurement process can lead to major implications down the line—cost overruns, machining failures, or misfits during assembly.
That’s why I’ve created this detailed, side-by-side comparison—to help you evaluate carbon steel vs cast iron based on real industrial priorities. From chemical composition and mechanical properties to casting behavior and post-processing needs, I’ll guide you through every factor that matters. By the end of this article, you’ll know exactly which metal suits your application—and why.
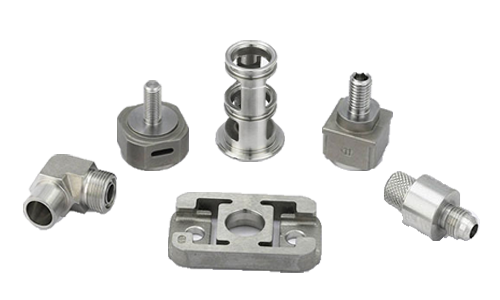
Get a quote now!
What Is Carbon Steel? Composition, Grades & Behavior
When discussing carbon steel vs cast iron, it’s important to first understand what carbon steel actually is. Carbon steel is a category of iron-carbon alloys where carbon is the primary alloying element, without significant amounts of other elements such as chromium, nickel, or molybdenum.
The carbon content typically ranges from 0.05% to 1.5%, which greatly influences the steel’s hardness, strength, and ductility. Carbon steel is known for its simplicity, cost-effectiveness, and adaptability across a wide range of industrial uses.
🔍 Classification of Carbon Steel by Carbon Content
Carbon steel is generally classified into three main types based on its carbon content:
- Low Carbon Steel (Mild Steel)
- Carbon content: up to 0.25%
- Soft, ductile, and easy to form or weld
- Common in basic structural components
- Medium Carbon Steel
- Carbon content: 0.25% to 0.6%
- Greater strength and hardness
- Used where a balance between strength and ductility is needed
- High Carbon Steel
- Carbon content: 0.6% to 1.5%
- Hard and wear-resistant
- Less ductile, and more challenging to machine or weld
Each grade behaves differently during processing and end-use, and the choice between them depends on the desired balance of strength, machinability, and formability.
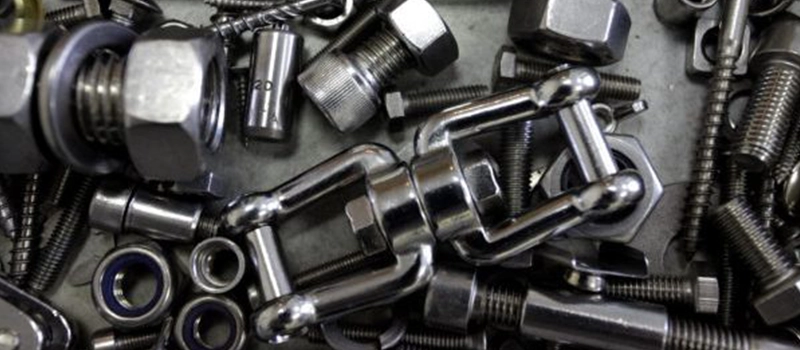
🔬 Typical Chemical Composition
Besides carbon, carbon steel may contain small amounts of:
- Manganese – improves hardenability and strength
- Phosphorus and sulfur – kept low to avoid brittleness
- Silicon – enhances deoxidation during steelmaking
The absence of large quantities of alloying elements distinguishes carbon steel from alloy steels and contributes to its affordability and wide availability.
What Is Cast Iron? Composition, Varieties & Behavior
To understand carbon steel vs cast iron, we must look at what makes cast iron fundamentally different. Like carbon steel, cast iron is an iron-carbon alloy—but with a significantly higher carbon content, typically ranging from 2.0% to 4.0%. This increase in carbon changes everything: structure, behavior, strength, and performance.
In cast iron, the excess carbon doesn’t dissolve into the iron matrix. Instead, it forms graphite flakes, nodules, or cementite, depending on the type of cast iron and the cooling rate during solidification. These carbon forms create distinct microstructures that give cast iron its unique properties—most notably, its excellent castability and high compressive strength.
🔍 Main Types of Cast Iron
There are several varieties of cast iron used in industrial manufacturing, each with distinct characteristics:
- Gray Cast Iron
- Contains graphite flakes
- Excellent damping capacity
- Easily cast and machined
- Most commonly used type
- Ductile (Nodular) Cast Iron
- Graphite forms as nodules (spheroidal graphite)
- Improved tensile strength and ductility
- Common in pressure-containing parts
- White Cast Iron
- Carbon forms cementite instead of graphite
- Hard and wear-resistant, but brittle
- Used for abrasion-resistant surfaces
- Malleable Cast Iron
- Heat-treated white cast iron
- Better ductility and toughness than gray or white iron
- Often used for small, impact-prone components
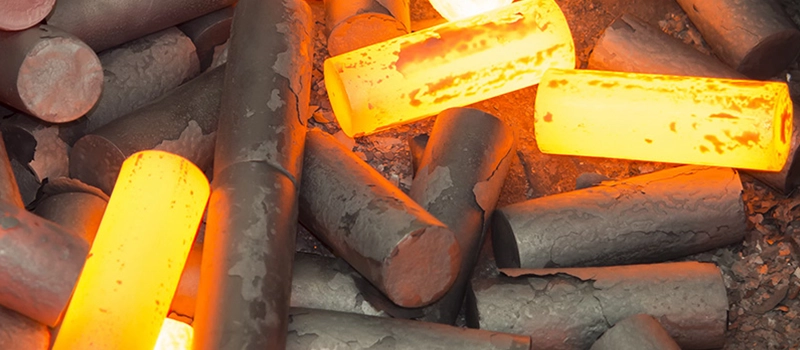
🧪 Chemical Makeup and Additives
In addition to high carbon content, cast iron often includes:
- Silicon (1–3%) – promotes graphite formation
- Manganese – increases hardness
- Phosphorus and sulfur – may improve castability but reduce toughness
The presence and interaction of these elements, especially carbon and silicon, determine the type of cast iron and its microstructure. Compared to carbon steel, cast iron’s carbon is present in a free form (graphite) rather than being entirely dissolved, which is why its physical behavior is so different.
Carbon Steel vs Cast Iron: Mechanical and Structural Comparison
When it comes to selecting materials for heavy-duty industrial components, understanding the mechanical differences in carbon steel vs cast iron is essential. These two metals may look similar, but they behave very differently under stress, impact, and load-bearing conditions. This section offers a head-to-head comparison of carbon steel vs cast iron in terms of structural performance.
🔩 Strength and Tensile Behavior in Carbon Steel vs Cast Iron
One of the most important factors in evaluating carbon steel vs cast iron is how each material handles tensile and compressive forces.
- Carbon steel demonstrates high tensile strength, making it suitable for parts subjected to stretching, bending, or pulling forces. It resists breaking even under extreme load and can be further strengthened through heat treatment.
- Cast iron, by contrast, excels in compressive strength but performs poorly in tension. It tends to crack or break under bending or shock loads due to its brittle nature.
So in the context of carbon steel vs cast iron, choose carbon steel when tensile stress or dynamic forces are a concern.
🧱 Ductility and Toughness: Carbon Steel vs Cast Iron in Impact Resistance
Another critical comparison in carbon steel vs cast iron is ductility—the ability of a material to deform without breaking.
- Carbon steel is highly ductile, especially in low and medium carbon forms. It can bend or stretch without fracturing, offering more flexibility in structural applications.
- Cast iron lacks ductility due to its graphite-based structure. It fractures suddenly, often without warning signs, making it risky for applications that experience vibration or shock.
This highlights a key difference in carbon steel vs cast iron: carbon steel absorbs energy, while cast iron tends to fail under impact.
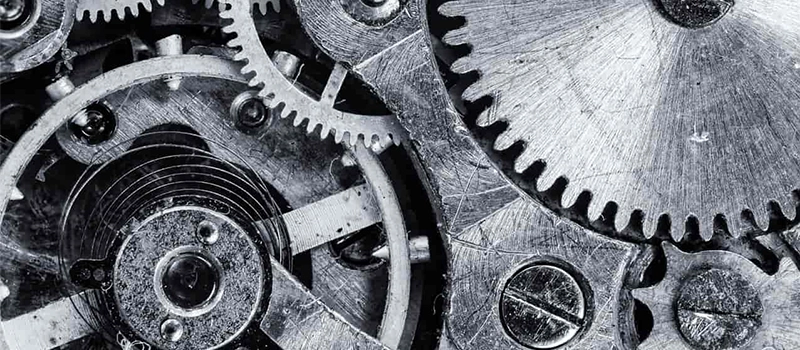
⚙️ Hardness and Wear Resistance: A Key Contrast in Carbon Steel vs Cast Iron
The hardness and surface durability of the material also influence your decision between carbon steel vs cast iron.
- Cast iron—particularly white and high-chromium grades—offers exceptional hardness and wear resistance. It’s ideal for surfaces exposed to abrasion, such as bearing housings, brake discs, and liners.
- Carbon steel, while not as hard in its untreated form, can still achieve high hardness through heat treatment. However, it is generally less wear-resistant compared to cast iron in raw form.
In the battle of carbon steel vs cast iron for wear-heavy applications, cast iron wins—but only if brittleness is not a concern.
📏 Fracture Behavior and Elongation: Carbon Steel vs Cast Iron in Failure Modes
Another vital point of comparison in carbon steel vs cast iron is how each material fails under load.
- Carbon steel typically shows elongation before fracture, meaning it stretches or deforms first. This provides warning before mechanical failure.
- Cast iron fails brittly and suddenly, with little to no elongation. This type of failure can be catastrophic if not properly engineered into the design.
This behavior strongly favors carbon steel vs cast iron in safety-critical or high-vibration applications.
📊 Comparison Table: Carbon Steel vs Cast Iron
Property | Carbon Steel | Cast Iron |
---|---|---|
Carbon Content | 0.05%–1.5% | 2.0%–4.0% |
Tensile Strength | High | Low to Moderate |
Compressive Strength | Moderate | High |
Ductility | High | Low (Brittle) |
Wear Resistance | Moderate | High |
Elongation Before Fracture | Present | Absent |
Shock Resistance | Excellent | Poor |
Fracture Behavior | Gradual | Sudden |
💡 Final Thoughts on Carbon Steel vs Cast Iron in Structural Use
In summary, carbon steel vs cast iron shows distinct differences in how each material handles stress, shock, and structural load:
- Choose carbon steel for tensile strength, impact resistance, and safety
- Choose cast iron for compressive loads, wear resistance, and dimensional stability
Understanding these mechanical contrasts between carbon steel vs cast iron helps engineers, designers, and procurement teams make decisions that reduce failure risk and improve overall performance.
Carbon Steel vs Cast Iron in Processing—Machinability & Weldability
Beyond mechanical performance, the way a material behaves during manufacturing processes like machining and welding can have a direct impact on production time, tooling cost, and quality control. Understanding carbon steel vs cast iron from a processing perspective is essential for both design engineers and buyers.
🔧 Machinability: Carbon Steel vs Cast Iron
Machinability refers to how easily a material can be cut, drilled, milled, or shaped using tools.
- Cast iron is generally easier to machine than carbon steel, especially gray cast iron. The graphite in its microstructure acts like a built-in lubricant, reducing friction and allowing tools to cut smoothly.
- Carbon steel, particularly in higher carbon grades, is tougher and more abrasive to tools. It can generate higher cutting forces, more heat, and increased tool wear—especially if not using optimized speeds and feeds.
However, low-carbon steels are easier to machine than high-carbon ones, and surface finish tends to be cleaner with carbon steel when properly tooled.
Summary: In the comparison of carbon steel vs cast iron, cast iron wins in machinability, especially for large-volume, low-complexity parts.
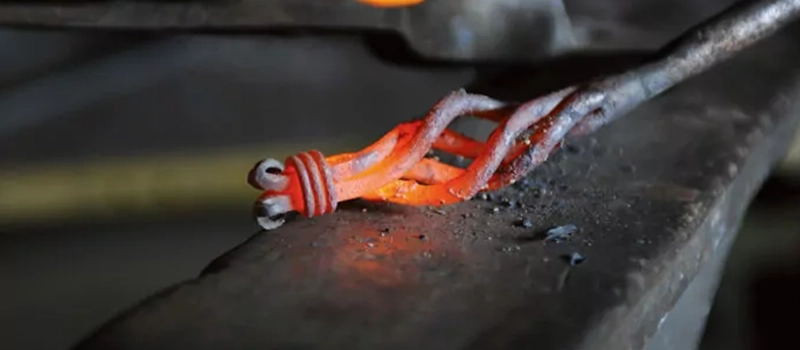
🔩 Weldability: A Clear Winner in Carbon Steel vs Cast Iron
Weldability is one of the most critical considerations in metal selection—especially for structural and assembled components.
- Carbon steel, especially low-carbon grades, is very weldable using common techniques like MIG, TIG, or arc welding. It doesn’t require preheating or special handling in most cases.
- Cast iron is notoriously difficult to weld. It requires pre-heating, slow cooling, and specialized filler materials to avoid cracking and distortion. The graphite in cast iron causes localized weakening and uneven heat flow, which often leads to internal stress buildup.
Summary: For assemblies requiring welding, carbon steel is vastly superior to cast iron in both convenience and reliability.
🛠️ Tooling and Production Cost Considerations
From a cost perspective:
- Cast iron can reduce machining time and increase tool life, but welding limitations may increase fabrication complexity.
- Carbon steel may require more effort in machining, but allows for flexible fabrication, onsite adjustments, and strong welded joints.
This makes carbon steel vs cast iron a trade-off in terms of process compatibility and total manufacturing cost. The right choice depends on your design intent, assembly methods, and available equipment.
📌 Key Takeaways: Carbon Steel vs Cast Iron in Processing
Processing Aspect | Carbon Steel | Cast Iron |
---|---|---|
Machinability | Moderate to Low (varies) | High (especially gray iron) |
Weldability | Excellent | Poor |
Tool Wear | Higher | Lower |
Fabrication Flexibility | High | Low |
Risk of Cracking | Low | High (especially post-welding) |
💡 Conclusion: Which to Choose for Manufacturing Efficiency?
When considering carbon steel vs cast iron from a processing perspective:
- Choose cast iron for parts that are machined but not welded—such as housings, blocks, and bases
- Choose carbon steel for parts that require welding, forming, or complex fabrication
Casting and Forging Behavior: What You Must Know
In the manufacturing world, the choice between carbon steel vs cast iron isn’t just about the final product—it starts with how the material behaves during forming, especially casting and forging. These two metals respond very differently to heat, mold design, and post-processing. A smart material choice here can save time, reduce defects, and improve dimensional accuracy.
🏗️ Casting Behavior: Carbon Steel vs Cast Iron
Casting is a fundamental process in industrial production, and cast iron is known for its superior castability.
- Cast iron has excellent fluidity when molten. Its high carbon and silicon content allow it to fill complex mold cavities with minimal turbulence. This makes it ideal for producing intricate or thick-walled components with consistent dimensional accuracy.
- Carbon steel, however, is more difficult to cast. Its higher melting temperature (around 1425–1540°C compared to cast iron’s ~1200–1300°C) and lower fluidity mean it requires more energy, better mold design, and tighter process control.
Moreover, carbon steel is more prone to shrinkage and internal defects, such as porosity or inclusions, if not properly handled.
Summary: In casting, cast iron outperforms carbon steel in ease, efficiency, and mold accuracy.
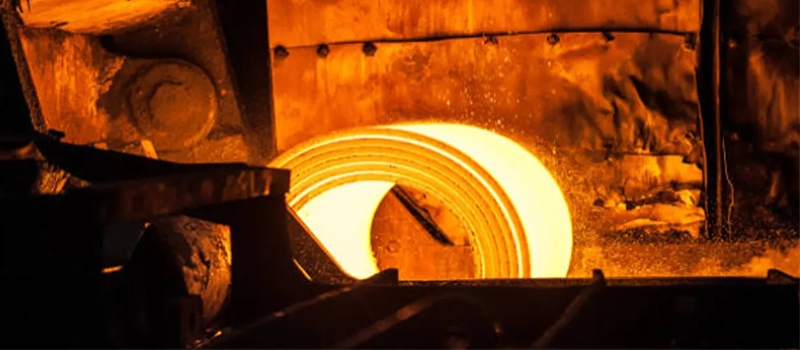
🔨 Forging Behavior: Carbon Steel vs Cast Iron
Forging is where carbon steel pulls far ahead in the carbon steel vs cast iron debate.
- Carbon steel can be hot-forged or cold-forged into a wide range of shapes. Its toughness, ductility, and grain refinement under pressure make it suitable for high-stress applications, such as axles, crankshafts, and load-bearing brackets.
- Cast iron, due to its brittle nature, cannot be forged. It fractures rather than deforms under forging loads, making it unsuitable for any process involving high mechanical pressure.
Forging improves the internal grain structure and mechanical properties of carbon steel—making it both stronger and more reliable than a cast equivalent in certain applications.
🧱 Mold and Tooling Considerations
From a tooling perspective:
- Cast iron requires less pressure and simpler molds due to its fluidity. Sand casting and shell molding are common.
- Carbon steel casting demands stronger molds, more refined gating systems, and careful cooling control.
Meanwhile, carbon steel forging requires precise presses or hammers and controlled heating, but the end result is a part with superior grain structure and fatigue resistance.
📌 Quick Comparison: Casting & Forging – Carbon Steel vs Cast Iron
Behavior Aspect | Carbon Steel | Cast Iron |
---|---|---|
Castability | Moderate to Low | Excellent |
Casting Temperature | High (~1425–1540°C) | Lower (~1200–1300°C) |
Fluidity | Lower | High |
Shrinkage Risk | Higher | Lower |
Forging Capability | Excellent | Not suitable |
Grain Structure Post-Forming | Refined under forging | No improvement through casting only |
Need Help? We’re Here for You!
💡 Bottom Line: Which Forming Method Fits Your Project?
In summary:
- Choose cast iron for complex-shaped parts with minimal machining and no need for forging
- Choose carbon steel when forging is required or when mechanical strength must be maximized
Understanding casting and forging differences in carbon steel vs cast iron helps you plan smarter from the design stage to the production floor.
Industrial Applications: Where Each Metal Excels
In the ongoing comparison of carbon steel vs cast iron, one of the most practical questions is: where should each material be used? The answer depends on the specific demands of your project—mechanical stress, environmental exposure, required shape complexity, and production method all play a role.
Both carbon steel and cast iron have carved out essential roles across key industrial sectors. Below is a breakdown of where each material performs best, based on its strengths.
🏭 Applications of Carbon Steel in Industry
Thanks to its strength, ductility, and weldability, carbon steel is widely used in components that must endure tension, impact, or cyclic loading. It’s especially favored where fabrication flexibility, structural integrity, or post-processing is required.
Typical industrial uses of carbon steel:
- Construction Industry
- Structural beams, reinforcement bars, and brackets
- Welded frames and load-bearing assemblies
- Automotive & Transportation
- Drive shafts, suspension components, chassis frames
- Forged gears, axles, and connecting rods
- Petrochemical and Energy
- Piping systems, pressure vessels, flanges
- Pipe supports and bracketry
- Agriculture & Heavy Equipment
- Hydraulic arms, levers, mounting brackets
- Forged attachments for tilling and harvesting
Why it fits: Carbon steel’s mechanical strength and adaptability make it the material of choice when reliability and long-term structural performance are priorities.
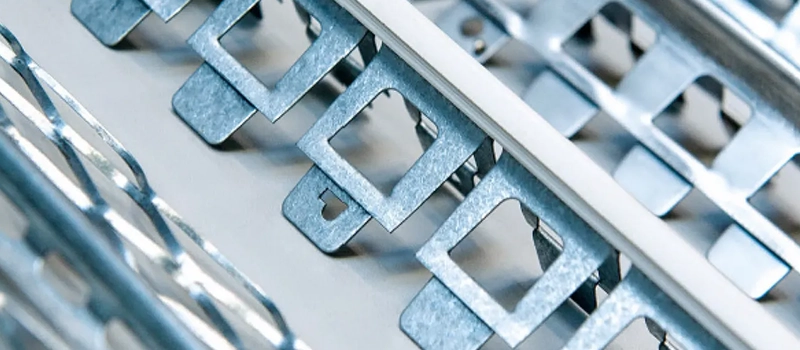
⚙️ Applications of Cast Iron in Industry
Cast iron excels in applications requiring rigidity, compressive strength, and wear resistance—particularly for parts that are thick, stationary, or cast in complex shapes. Its excellent fluidity during casting allows it to form intricate geometries that would be difficult or costly to machine from solid bar stock.
Typical industrial uses of cast iron:
- Machinery & Tooling Bases
- Lathe beds, milling machine frames
- Mounting plates and machine columns
- Automotive Industry
- Engine blocks, cylinder heads
- Brake discs, drums, and manifolds
- Water and Waste Infrastructure
- Pipe fittings, manhole covers, valve bodies
- Pump housings and impellers
- Mining & Crushing Equipment
- Liner plates, wear parts, housings
Why it fits: Cast iron is ideal for components that require vibration damping, high compressive strength, and durable cast shapes.
🧭 Choosing Based on Application: Carbon Steel vs Cast Iron
Here’s a quick guide for matching material to project need:
Application Type | Recommended Material |
---|---|
Structural welding and fabrication | Carbon Steel |
Load-bearing shafts or rotating parts | Carbon Steel |
Static, complex-shaped, thick components | Cast Iron |
Abrasive surface or wear-resistant parts | Cast Iron (white or ductile) |
Components requiring frequent repair | Carbon Steel (weldable) |
Parts with tight casting tolerances | Cast Iron |
Forged or hot-formed mechanical parts | Carbon Steel |
💡 Final Word: Function First in Carbon Steel vs Cast Iron Selection
There is no universal winner in the carbon steel vs cast iron debate. Each material shines in the right context. The key is to align your choice with the demands of the application—mechanical load, manufacturing method, and performance expectation.
Cost Comparison: Carbon Steel vs Cast Iron in Real-World Budgets
When comparing carbon steel vs cast iron, cost is always a top consideration—especially for industrial buyers managing tight production schedules and procurement budgets. But price isn’t just about the raw material cost. You also need to evaluate processing expenses, machining time, tool life, yield loss, and long-term durability.
This section breaks down the total cost of ownership for both materials from a manufacturer’s perspective.
💲 Raw Material Cost: Carbon Steel vs Cast Iron
- Cast iron is generally cheaper per kilogram than carbon steel. It has a lower melting point, requires less refining, and is often produced using recycled scrap iron, which keeps costs low.
- Carbon steel, especially in medium to high-carbon grades, tends to be more expensive due to additional processing steps and higher energy requirements.
However, the raw material price is only the starting point.
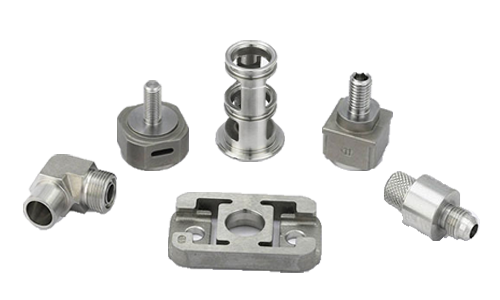
Get a quote now!
🛠️ Processing and Manufacturing Costs
Casting Costs:
- Cast iron’s superior fluidity reduces casting defects and mold complexity.
- Carbon steel requires higher temperatures, stronger molds, and tight process control, which increases energy usage and labor time.
Machining Costs:
- Cast iron machines easily, wears tools slowly, and reduces cycle time.
- Carbon steel, particularly higher grades, generates more tool wear, heat, and chip volume—raising machining costs.
Welding and Fabrication:
- Carbon steel is easy and inexpensive to weld, reducing fabrication costs.
- Cast iron requires preheating, special rods, and slow cooling, making welding repairs costly and complex.
🔧 Tooling, Scrap, and Yield Loss
- Cast iron offers good dimensional stability, which improves mold yields and reduces scrap rates in casting.
- Carbon steel may experience higher shrinkage or inclusions during casting, potentially increasing rework or scrap losses.
In contrast, forged carbon steel parts tend to be more reliable with tighter tolerances—reducing secondary machining or fitting issues.
🧪 Lifecycle and Replacement Cost
One key factor often overlooked is material longevity. While cast iron is cheaper upfront, it may crack under dynamic loads, requiring premature replacement.
Carbon steel, particularly when heat-treated, often offers a longer service life, especially in high-stress or impact applications. This can offset higher upfront costs by lowering downtime and replacement frequency.
📊 Cost Summary Table: Carbon Steel vs Cast Iron
Cost Factor | Carbon Steel | Cast Iron |
---|---|---|
Raw Material Cost | Moderate to High | Low |
Casting Efficiency | Moderate (more control) | High |
Machining Cost | Higher (tool wear) | Lower (easy cutting) |
Welding & Fabrication | Low (easy to weld) | High (complex to weld) |
Tooling & Mold Expense | High | Low |
Scrap/Rework Risk | Moderate to High | Low |
Lifecycle Replacement | Longer (impact durable) | Shorter (brittle failure) |
💡 Final Thoughts on Cost: Value Over Price
When evaluating carbon steel vs cast iron from a cost perspective:
- Choose cast iron if your goal is low-cost casting for static parts with minimal fabrication.
- Choose carbon steel if the part requires welding, impact resistance, or long-term durability.
While cast iron may win on raw material and casting cost, carbon steel often delivers better overall value, especially in high-performance environments where lifecycle costs matter.
Environmental and Compliance Considerations
As sustainability and regulatory compliance become increasingly important in global sourcing, understanding the environmental footprint of carbon steel vs cast iron is essential—especially for buyers exporting to regions like the EU, North America, or Japan. Material selection not only affects product performance but also influences your ability to meet environmental standards and certifications.
🌍 Environmental Impact of Carbon Steel vs Cast Iron
Raw Material Sourcing and Energy Use:
- Cast iron production typically involves recycled scrap iron, which helps reduce its environmental footprint. Its lower melting temperature (~1200–1300°C) also means less energy consumption during casting.
- Carbon steel, while also recyclable, requires more refined processing. Its higher melting point (1425–1540°C) increases energy demands, especially in foundry and forging operations.
CO₂ Emissions:
- The carbon footprint of carbon steel is slightly higher than cast iron per ton of production due to energy-intensive refining, especially in higher-grade steels.
- However, forged carbon steel parts tend to last longer under load, meaning fewer replacements and less waste, which can offset emissions over the product lifecycle.
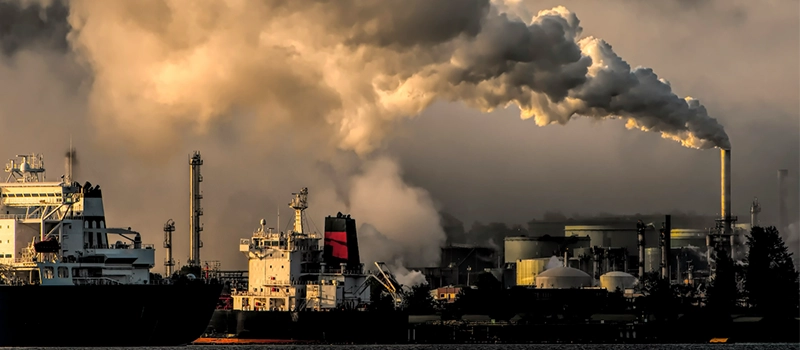
🔄 Recyclability and Waste Management
Both carbon steel and cast iron are fully recyclable, and both materials are widely reclaimed and reused in the industrial ecosystem.
- Cast iron scrap is easy to remelt and reuse in foundries.
- Carbon steel is also highly recyclable, with minimal degradation in mechanical properties after remelting.
The key difference is that carbon steel scrap is often segregated by grade to preserve quality, whereas cast iron recycling is more straightforward due to its generic composition.
📜 Compliance and Industry Certifications
When evaluating carbon steel vs cast iron from a compliance standpoint, both materials can meet international standards—but it’s important to verify supplier credentials.
Common Standards and Requirements:
- CE (Conformité Européenne) – Required for metal components used in European markets
- REACH and RoHS – Regulate hazardous substances in metal alloys
- ISO 9001 / ISO 14001 – Relate to quality and environmental management systems
- ASTM / JIS / DIN – Material-specific standards for chemical and mechanical properties
For exports to the EU, manufacturers must have a registered EU Authorized Representative (EC REP) to handle compliance documents and liability. Products made of carbon steel or cast iron must also be accompanied by material certificates, safety data sheets, and inspection reports.
⚖️ Environmental Summary Table: Carbon Steel vs Cast Iron
Factor | Carbon Steel | Cast Iron |
---|---|---|
Melting Energy | Higher | Lower |
CO₂ Emissions per Ton | Moderate to High | Moderate |
Recyclability | Excellent | Excellent |
Lifespan in Use | Long (impact-resistant) | Moderate (brittle failure) |
Material Certification Access | Widely documented | Widely documented |
EU/REACH/CE Compliance | Standardized | Standardized |
💡 Final Consideration: Responsibility in Material Selection
In the context of carbon steel vs cast iron, both materials offer strong recyclability and are globally recognized in industrial compliance systems. However:
- Choose cast iron for low-energy casting with minimal post-processing
- Choose carbon steel for high-performance parts with longer service life and international compliance flexibility
As regulations tighten and sustainability becomes a differentiator, understanding these material-level impacts is key to making responsible, globally compliant sourcing decisions.
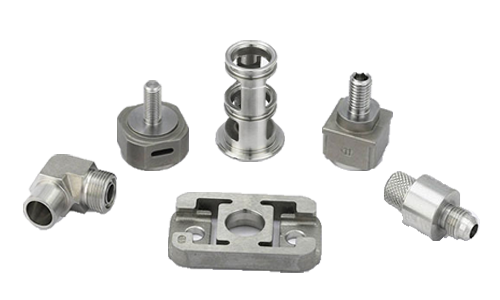
Get a quote now!
How to Choose Between Carbon Steel vs Cast Iron for Industrial Projects
After reviewing all the differences in composition, mechanical behavior, process compatibility, cost, and compliance, the final step is clear: how do you decide which material truly fits your industrial needs?
The carbon steel vs cast iron decision isn’t one-size-fits-all. It depends on multiple factors—each tied to your part’s function, environment, and production method. In this section, we’ll walk through a clear, actionable framework for making the right material choice.
🧠 Step 1: Define Your Primary Performance Requirement
Ask yourself: what must this part do?
- Will it carry tensile loads or be exposed to shock?
→ Choose carbon steel (superior ductility and impact resistance) - Will it be under compressive force with minimal movement?
→ Choose cast iron (high compressive strength, dimensional stability) - Does the part require welding or on-site repair?
→ Carbon steel is easy to weld, cast iron is difficult to weld
⚙️ Step 2: Evaluate Processing and Manufacturing Capabilities
Match the material to your production methods:
- Complex shapes with fine detail?
→ Cast iron is ideal for intricate castings - Need forging, bending, or post-machining?
→ Carbon steel supports forming and machining flexibility - High production volumes with tight tolerances?
→ Consider machinability and casting shrinkage of each metal
💸 Step 3: Consider Total Cost, Not Just Raw Material
Remember, the lowest unit price doesn’t always mean the lowest total cost.
- Cast iron has a lower upfront cost, especially in high-volume casting
- Carbon steel may have higher processing costs, but offers better lifecycle performance
- Think in terms of replacement cycles, tool wear, and post-processing
📦 Step 4: Think About Weight and Transportation
Material weight affects freight cost and design viability.
- Cast iron is denser, heavier, and better at damping vibration
- Carbon steel offers strength at a lower weight, which may reduce transport and installation costs
🧾 Step 5: Check for Compliance & Certification Needs
Will the part be used in regulated markets like the EU or North America?
- Both carbon steel and cast iron can meet CE, REACH, RoHS, and ISO standards
- But carbon steel often has broader weldability, making it easier to pass structural integrity checks after assembly
Final Advice: Align Your Choice with Function + Process
In the end, the carbon steel vs cast iron decision is not about better or worse—it’s about fit for purpose. The more clearly you define how your part will be used, how it will be made, and what it must withstand, the easier it becomes to choose the right material.
Conclusion: Our Expert Recommendation on Carbon Steel vs Cast Iron
When it comes to carbon steel vs cast iron, there’s no universal winner—only the best fit for your project’s specific needs. Each material has distinct advantages:
- Carbon steel offers superior weldability, tensile strength, and long-term durability—ideal for structural, forged, and fabricated parts.
- Cast iron provides excellent castability, compressive strength, and wear resistance—perfect for stable, complex-shaped components.
The smartest choice depends on your design, processing methods, performance expectations, and compliance requirements.
At Dalian ZhongSheng Metal Products, we understand these decisions aren’t always easy. With over 30 years of experience in casting, machining, forging, and sheet metal fabrication, our team supports global buyers—especially from North America, Europe, Japan, and South Korea—by helping them select the most suitable materials based on technical drawings, tolerance specs, and cost targets.
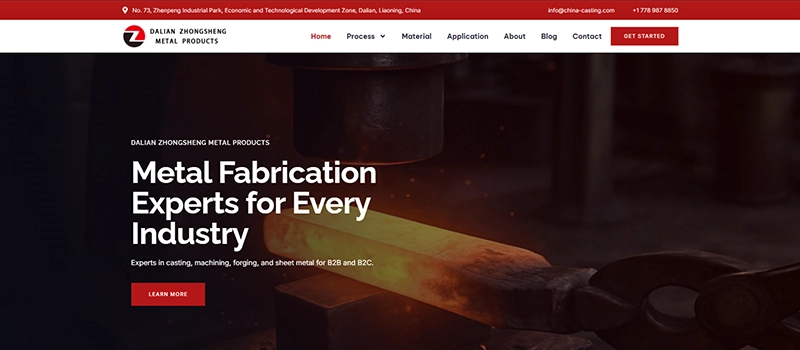
As a certified manufacturer with CE and EU Representative registration, we not only guarantee quality but also assist our clients in solving their toughest sourcing challenges—whether it’s material substitution, defect prevention, or balancing quality with price.
We operate five full-scale production lines and provide:
- One-stop sourcing for carbon steel and cast iron parts
- Custom solutions based on your drawings and application
- Strict quality inspection and global logistics support
- Professional service from quotation to delivery
💬 Have a project in mind?
Send your drawings or RFQs to us at marketings@china-casting.com. Our engineering team will help you evaluate the right material, process, and timeline—so you can manufacture with confidence.