Are you struggling to decide between 304 vs 316 stainless steel? Unsure which grade offers better corrosion resistance, especially in marine or chemical environments? Worried that choosing the wrong material could lead to premature failure, added costs, or rejected shipments? Is 316 stainless steel really worth the higher price—or is 304 good enough for your project? Not clear on the difference between 304 and 316 stainless steel when it comes to strength, durability, and food-grade safety? Wondering how to tell them apart or when to use each one?
Both 304 and 316 stainless steel are widely used in metal fabrication, but they serve different needs.
304 stainless steel is more cost-effective and works well in dry, indoor, or general-purpose applications. 316 stainless steel, enhanced with molybdenum, offers superior corrosion resistance and is ideal for coastal, chemical, or high-moisture environments. Choosing the right one depends on where and how the material will be used.
Don’t make the mistake of choosing based on price alone—what you save upfront could cost you much more later. Let’s break down the key differences between 304 vs 316 stainless steel so you can make a confident, informed decision.
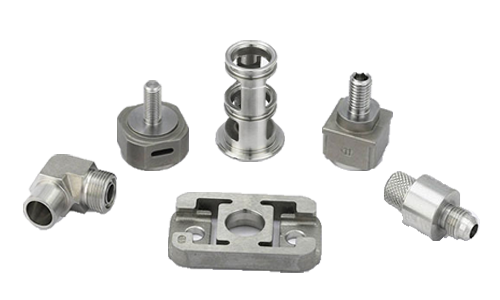
Get a quote now!
What Is Stainless Steel and Why Alloy Grade Matters
Stainless steel is used everywhere—from kitchenware and construction materials to automotive parts and medical equipment. But while all stainless steels resist rust, not all of them perform the same way. That’s why understanding what makes each grade different is essential for choosing the right material for your project—especially when comparing 304 vs 316 stainless steel.
Stainless steel is defined by its chromium content—at least 10.5%, which creates a thin, invisible oxide layer that protects the metal from corrosion. This makes it a strong candidate for environments where moisture, chemicals, or high humidity are present.
But stainless steel isn’t just chromium and iron. Other alloying elements are added in precise amounts to achieve specific properties. For example:
- Nickel improves toughness and flexibility
- Molybdenum boosts resistance to harsh chemicals and saltwater
- Carbon adjusts strength and hardness
- Manganese and nitrogen can improve strength or reduce cost
These ingredients are what separate one grade from another—and even small differences in composition can affect how a stainless steel behaves in welding, machining, or corrosive environments. This is especially important when choosing between 304 vs 316 stainless steel, which are often specified for very different end uses.
Why the 300 Series Stainless Steels Are So Common
One of the most widely used families of stainless steel is the 300 series. These are known as austenitic stainless steels, meaning they have a non-magnetic crystal structure and excellent resistance to corrosion and heat.
The 300 series is especially known for:
- High weldability and formability
- Good strength under normal temperatures
- Excellent resistance to oxidation and most common acids
- Suitability for food-grade, marine, and structural applications
The most popular grades in this family are 304 and 316 stainless steel. While they share many characteristics, their performance in harsh environments can be quite different. If you’re sourcing materials for industrial parts, food processing, or outdoor equipment, knowing the differences between 304 vs 316 stainless steel can help you make the right material choice from the start.
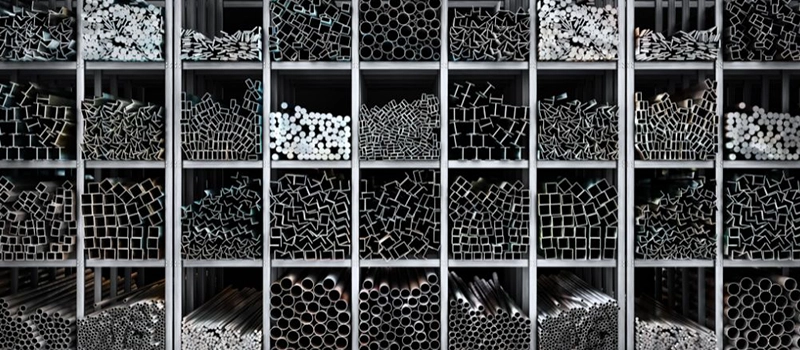
In-Depth Comparison: 304 vs 316 Stainless Steel Performance
Though similar in appearance, 304 vs 316 stainless steel differs significantly in performance across a range of categories. These differences can affect how the material handles corrosion, heat, mechanical stress, and fabrication.
Here’s a detailed look at the functional and physical properties that separate these two industry-standard stainless steels.
Corrosion Resistance
This is the most well-known and critical difference. Both 304 and 316 stainless steel resist rust and corrosion, but 316 outperforms 304 in aggressive environments—particularly those with:
- Chlorides (e.g. saltwater, de-icing salts)
- Acids and harsh industrial chemicals
- Coastal or marine exposure
- Continuous contact with cleaning agents
This advantage comes from the 2–3% molybdenum content in 316 stainless steel, which strengthens its passive oxide layer and reduces the risk of:
- Pitting corrosion
- Crevice corrosion
- Surface breakdown in saline environments
304 stainless steel, while still corrosion-resistant, can show signs of wear or staining in similar conditions over time.
Chemical Composition
Element | 304 Stainless Steel | 316 Stainless Steel |
---|---|---|
Chromium | ~18% | ~16% |
Nickel | ~8% | ~10% |
Molybdenum | None | ~2–3% |
Carbon | ≤ 0.08% | ≤ 0.08% |
This minor change in formulation, particularly the addition of molybdenum, is what enables 316 to resist chlorides, sulfates, and acids more effectively than 304.
Temperature Resistance
Both materials perform well under moderate to high heat, but 316 has a slight advantage in thermal resistance, particularly when heat and corrosion act together.
- 304 stainless steel: Handles up to ~870°C (1600°F) in intermittent service
- 316 stainless steel: Slightly better oxidation resistance at elevated temperatures
Need Help? We’re Here for You!
316 is better suited for:
- Steam environments
- Heat exchangers
- Marine exhaust systems
For ultra-high-temperature applications, other grades (like 310) may be more appropriate.
Strength and Durability
In standard use, 304 vs 316 stainless steel shows similar tensile and yield strength. Both are durable, high-strength materials, but 316 may provide better resistance to fatigue and vibration in long-term or harsh settings.
Property | 304 SS | 316 SS |
---|---|---|
Tensile Strength (MPa) | ~505 | ~515 |
Yield Strength (MPa) | ~215 | ~205 |
Elongation (%) | ~70 | ~60–70 |
Brinell Hardness | ~201 | ~217 |
The difference in hardness and fatigue strength, though slight, can matter in applications involving repeated movement, structural stress, or impact.
Weldability
Both alloys are excellent for welding using TIG, MIG, or resistance techniques. This makes them ideal for industrial pipework, tanks, and custom-fabricated parts.
A few points of difference:
- 304 is easier to weld and more forgiving under typical conditions
- 316 may require post-weld cleaning or passivation when hygiene or corrosion control is critical (e.g. food, pharma, chemical plants)
Neither alloy hardens after welding, which is a benefit for shaping and further fabrication.
Machinability
When it comes to cutting, drilling, and CNC work, 304 stainless steel is generally easier to machine. This is due to the absence of molybdenum, which can make 316 slightly tougher on tooling and increase wear during extended runs.
- 304 is ideal for complex cuts or high-volume production
- 316 may require slower cutting speeds and more lubricant
- Both are prone to galling, so anti-seize compounds or specific cutting techniques are recommended
If your application involves tight tolerances, threading, or intricate geometry, machinability becomes an important factor to consider.
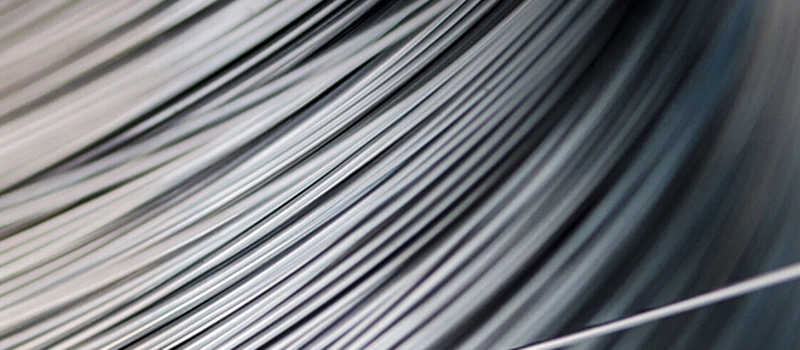
Magnetism and Physical Appearance
Visually, both 304 and 316 stainless steel appear similar—bright, smooth, and capable of high-polish finishes. However, their behavior around magnets differs:
- Both are non-magnetic in annealed form
- 304 can become slightly magnetic after cold working (bending, rolling, etc.)
- 316 remains more stable magnetically, which is important for electronic housings or lab environments
There is no visual way to distinguish the two without chemical testing, which is why proper documentation and material certification are key during procurement.
In summary, the technical differences between 304 vs 316 stainless steel affect how each performs in real-world conditions. From corrosion resistance and heat tolerance to weldability and machining ease, each alloy has a clearly defined role in modern fabrication.
When to Use 304 Stainless Steel
In the debate between 304 vs 316 stainless steel, many buyers find that 304 is more than enough for their project—especially when exposure to salt, harsh chemicals, or acids isn’t a major concern. Known for its excellent formability, weldability, and corrosion resistance, 304 stainless steel is often the most cost-effective and practical choice across a wide range of industries.
Ideal Environments for 304 Stainless Steel
304 stainless steel performs best in environments that are:
- Indoors or protected from harsh weather
- Low in chlorides (e.g., no seawater or salt exposure)
- Dry or moderately humid
- Clean and controlled (e.g., food processing or medical prep areas)
This makes 304 ideal for:
- Restaurant kitchens and food equipment
- Interior architectural railings, panels, and trim
- Home appliances like sinks, cooktops, dishwashers
- General-purpose tanks, enclosures, and machine parts
Because 304 stainless is easy to clean and sanitize, it’s also commonly used in pharmaceutical equipment, beverage production, and hospital settings—as long as those environments don’t include aggressive chemicals.
Need Help? We’re Here for You!
304’s Advantage in Fabrication
Between 304 vs 316 stainless steel, 304 is often the preferred material when large-scale fabrication is involved. It’s:
- Easier to bend, cut, and machine
- More forgiving during welding
- Less demanding on tools and labor
This makes it the go-to choice for manufacturers who need to produce:
- Sheet metal enclosures
- Support frames
- Customized brackets
- Piping systems that carry non-corrosive materials
If your team values speed, volume, and ease of processing, 304 provides an efficient route without compromising essential performance.
When 304 Is the Smarter Choice
Despite the benefits of 316, many engineers and buyers still choose 304 for:
- Indoor applications where moisture is minimal
- One-time installations with limited exposure
- Projects on a tighter budget that don’t demand marine-grade protection
- Non-chemical environments like dry storage, office buildings, or clean warehouses
In short, when you evaluate 304 vs 316 stainless steel for general-purpose projects, 304 often delivers the perfect balance of performance and affordability—as long as corrosion threats are low.
Industries That Commonly Use 304 Stainless Steel
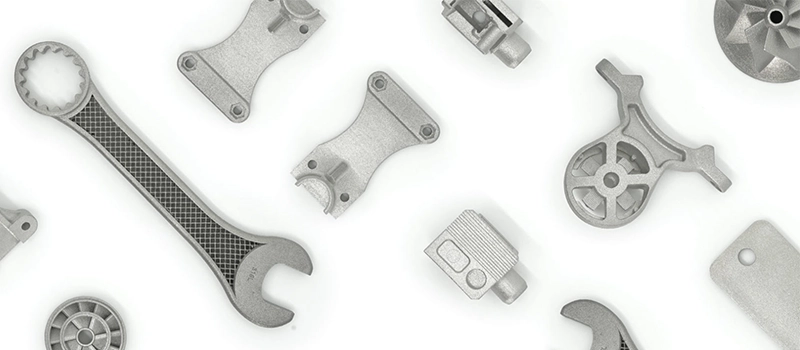
Many of the industries we serve here at Dalian ZhongSheng Metal Products rely on 304 stainless steel for its versatility and fabrication efficiency:
- Construction: Interior trim, support structures, elevator panels
- Food & Beverage: Tables, sinks, storage tanks, brewing equipment
- HVAC: Ducts, housings, air diffusers
- Consumer Products: Cookware, utensils, countertops
- Light Industrial: Conveyor frames, electrical cabinets, casings
Even if your application technically “could” benefit from 316, 304 often does the job well—especially if it won’t face salt, chemicals, or continuous dampness.
Choosing 304 in the 304 vs 316 stainless steel comparison often comes down to environment and efficiency. When the risks of corrosion are low and your project demands speed, workability, and clean aesthetics, 304 is an easy and reliable choice.
When to Use 316 Stainless Steel
If 304 stainless steel is the industry workhorse, then 316 is the specialist—designed for environments where corrosion resistance, chemical durability, and long-term performance are non-negotiable. When comparing 304 vs 316 stainless steel, 316 is the right choice when your application involves harsh exposure, saltwater, or chemically aggressive surroundings.
Superior Corrosion Resistance in Tough Conditions
The biggest advantage of 316 stainless steel is its resistance to chlorides and aggressive substances. Thanks to its added 2–3% molybdenum, 316 holds up in environments where 304 would eventually corrode or pit. That’s why engineers choose 316 for:
- Marine environments (saltwater, spray, humidity)
- Chemical processing plants (acids, solvents, alkalis)
- High-humidity or damp areas
- Sterile or sanitized settings where chemicals are regularly used
If your product will face de-icing salts, ocean spray, or chemical washdowns, 316 is the grade built to survive.
Applications That Demand 316 Stainless Steel
316 isn’t just for boats. It’s widely used across high-performance, long-lifespan industries where corrosion or contamination can’t be risked:
- Marine hardware: Fasteners, fittings, exhaust parts
- Food and beverage: Pasteurizers, sterilizers, high-saline storage
- Pharmaceuticals and labs: Processing equipment, surgical tools
- Oil and gas: Valve bodies, seals, offshore piping
- Architectural exteriors: Cladding, railings, fixtures near the coast
- Chemical tanks and piping: Systems exposed to acids, chlorides, or caustic agents
When evaluating 304 vs 316 stainless steel, this is where 316 truly earns its reputation: in places where failure from rust or corrosion could be costly or dangerous.
Better for Sanitation, Hygiene, and Repeated Washdowns
316 is often chosen in industries like biotech, food, beverage, and medical not just for corrosion resistance, but for its superior cleanliness under constant exposure to water and cleaning agents.
It tolerates:
- Chlorinated sanitizers
- Acetic, formic, citric, and phosphoric acids
- Steam and hot water
- Daily scrubbing or spraying
Because of this, you’ll often see 316 stainless steel in:
- Commercial kitchens and clean rooms
- Surgical-grade sinks and trays
- Dairy, brewing, and bottling plants
If hygiene and corrosion protection must coexist, 316 is the better choice in the 304 vs 316 stainless steel decision.
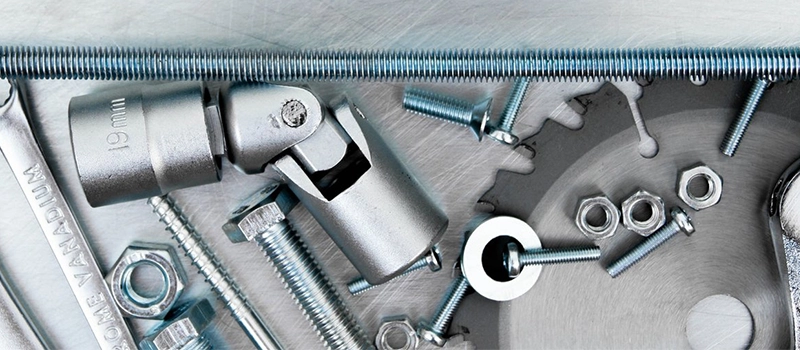
Material Longevity and Lifecycle Performance
316 stainless steel isn’t just about day-one performance. Its value comes from:
- Reduced maintenance costs
- Fewer replacements due to pitting or chemical damage
- Stronger resistance to long-term environmental fatigue
That’s why 316 is used in:
- Coastal construction projects
- Industrial facilities with corrosive exhaust
- Products expected to last 10–20 years without intervention
While 304 may be easier to machine or weld, 316 is the go-to for mission-critical applications, where integrity over time matters more than up-front fabrication convenience.
When 316 Is Clearly the Right Choice
Choose 316 stainless steel when:
- Your material will face chloride, moisture, or chemical exposure
- You need long service life with minimal maintenance
- The cost of failure is high (e.g., food contamination, structural rust, leakage)
- Sanitary regulations or cleaning cycles demand non-reactive surfaces
If you’re choosing between 304 vs 316 stainless steel, and corrosion is a real concern—not just a possibility—then 316 is the reliable, longer-lasting solution.
Cost Breakdown: 304 vs 316 Stainless Steel
When comparing 304 vs 316 stainless steel, performance is only half the equation—cost often plays an equally important role in material selection. While 316 clearly offers enhanced corrosion resistance and longevity in harsh conditions, it also comes with a higher price tag. Understanding the pricing logic behind these two alloys can help you make the right choice for both your project and your budget.
Why 316 Stainless Steel Is More Expensive
The price difference between 304 and 316 stainless steel mainly comes down to raw material content—specifically, molybdenum.
- 316 contains 2–3% molybdenum, which improves corrosion resistance but significantly increases cost
- Molybdenum is a volatile, high-value alloying element, and its price can fluctuate globally
- 316 also contains slightly more nickel, which further raises the overall base metal cost
As a result, 316 stainless steel is typically 20–35% more expensive than 304, depending on the market.
Note: Prices can shift based on global metal supply, demand, and even geopolitical factors affecting molybdenum production. Always request a live quote when sourcing large volumes.
Material vs Total Project Cost
The up-front price of stainless steel isn’t the only cost you should consider. The total cost of ownership also includes:
- Maintenance and replacement frequency
- Downtime due to corrosion failure
- Cleaning and sanitation procedures
- Regulatory compliance in food, pharma, or chemical applications
In dry, clean indoor environments, 304 is often the most economical choice. But in marine, food processing, or corrosive chemical settings, the longer service life of 316 can reduce your overall cost by minimizing failures and maintenance.
Cost-Saving Tips for Buyers
If you’re sourcing metal parts or fabricated components and trying to decide between 304 vs 316 stainless steel, here are some smart strategies to control costs:
- ✅ Mix grades within the same project: Use 316 only for the components exposed to moisture or corrosion, and 304 for the rest
- ✅ Request volume pricing: Larger batch orders reduce per-unit alloy costs, especially when buying directly from a factory like ours
- ✅ Ask for material certifications: Avoid overpaying for mislabelled or over-specified material
- ✅ Plan for life cycle, not just purchase price: 316 may save you more in the long term if your parts are hard to access or costly to replace
What Drives Stainless Steel Pricing Globally?
A few external factors that influence the cost difference between 304 vs 316 stainless steel include:
- Nickel and molybdenum market trends
- Export tariffs or trade restrictions
- Shipping and logistics cost fluctuations
- Scrap availability and recycling ratios
Keeping track of metal commodity trends—and working with a trusted supplier—can help you plan smarter and lock in better pricing windows.
In the context of 304 vs 316 stainless steel, 304 offers better affordability, especially for high-volume or general-purpose use. But when corrosion risk, hygiene, or longevity is critical, 316 becomes a strategic investment that pays off over time.
Common Misunderstandings About 304 vs 316 Stainless Steel
Despite being two of the most commonly used stainless steels, 304 vs 316 stainless steel is often misunderstood—especially by buyers unfamiliar with how small differences in composition can result in major differences in performance.
These misunderstandings can lead to:
- Overpaying for unnecessary material
- Underspecifying and causing early product failure
- Confusion during fabrication or inspection
Let’s clear up the most frequent myths.
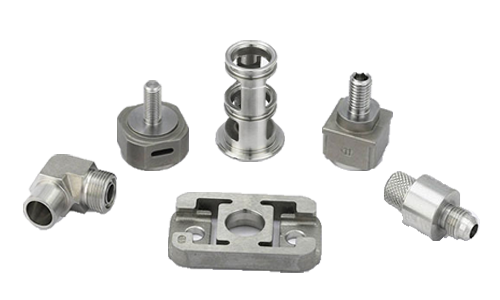
Get a quote now!
“304 vs 316 Stainless Steel Are Basically the Same” – False
On paper, 304 and 316 look similar. They’re both:
- Austenitic stainless steels
- Non-magnetic in annealed form
- Resistant to rust and corrosion
- Easy to weld and machine
But here’s the problem: assuming they are interchangeable can be costly.
The addition of molybdenum in 316 gives it much greater resistance to chlorides, acids, and industrial chemicals. If you use 304 in a marine or chemical environment assuming it’s “good enough,” you risk corrosion, pitting, and eventual failure—especially under long-term exposure.
“Use 316 for Everything—It’s Always Better” – Not True
Some buyers default to 316 because they think it’s “higher grade,” but that’s not always necessary.
In the 304 vs 316 stainless steel decision, context matters. If you’re producing indoor food equipment, architectural trim, or general-purpose machine parts, 304 offers nearly identical performance at a lower price and easier fabrication.
Using 316 in low-risk environments may just increase costs without adding real value.
“If It Looks Stainless, It’s Probably 304 or 316” – Dangerous Assumption
Visual inspection is not enough to identify stainless steel grade. Both 304 and 316 have the same bright silver finish and can be polished or brushed similarly. This leads some buyers to think they can spot the difference by eye—which is not true.
To confirm material grade, you need:
- Material certifications (e.g. Mill Test Reports)
- Spectrometer testing (PMI)
- Supplier declaration with composition breakdown
Failing to verify the grade can result in wrong installations, compliance failures, or warranty issues, especially in critical environments like pharmaceuticals or food production.
“All Stainless Steel Is Non-Magnetic” – Not Always
In the 304 vs 316 stainless steel comparison, both are non-magnetic in annealed form. But cold-working (bending, forming, or machining) can cause 304 to become slightly magnetic, while 316 remains more stable.
This is an important distinction for:
- Electronics enclosures
- Magnetic field-sensitive installations
- Laboratory and medical equipment
Don’t rely solely on magnet tests to identify the material or judge suitability.
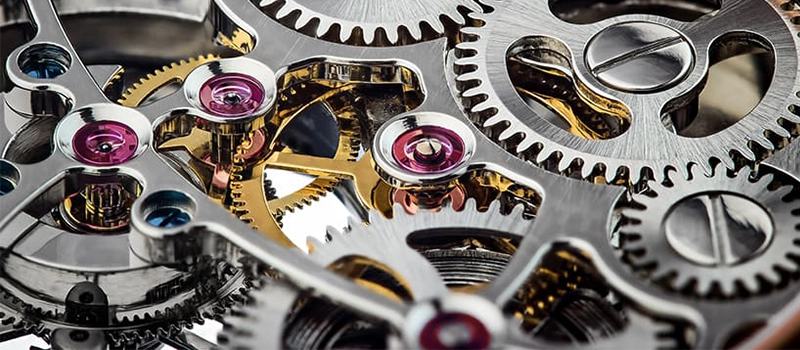
“Corrosion Means It’s Not Real Stainless” – Oversimplified
Stainless steel can still rust—especially if:
- It’s exposed to salt, chlorides, or acids
- It’s improperly cleaned (e.g., chlorinated bleach)
- It’s installed in crevice-prone or unventilated areas
If a buyer sees corrosion on 304 stainless steel in a marine environment and concludes it’s “low-quality,” the issue is usually mismatched application—not faulty steel.
Matching the material to the right environment is key in the 304 vs 316 stainless steel choice. Corrosion isn’t always a sign of fake steel—it’s a sign of inappropriate grade selection.
Clearing up these myths not only improves sourcing decisions but also helps prevent expensive failures, rework, or disputes with customers. Understanding the real science behind 304 vs 316 stainless steel is what turns good decisions into great ones.
Confidently Choosing Between 304 vs 316 Stainless Steel
When deciding between 304 vs 316 stainless steel, the choice comes down to application environment and performance expectations.
Use 304 stainless steel when you need durability, affordability, and ease of fabrication in low-corrosion settings. It’s perfect for general-use components, interior applications, and dry environments.
Use 316 stainless steel when your products will face salt, moisture, chemicals, or hygiene-sensitive operations. Its added molybdenum makes it stronger in aggressive conditions and ideal for long-term performance.
Even though the differences in 304 vs 316 stainless steel may seem small on paper, in real-world conditions they impact product lifespan, safety, and maintenance costs.
At Dalian ZhongSheng Metal Products, we’ve spent over 30 years helping customers choose the right grade for their project needs—backed by certified materials, in-house production, and expert guidance.
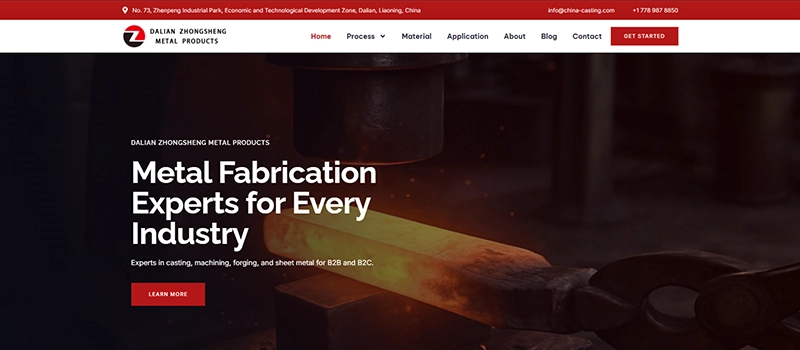
Whether you’re sourcing castings, machined parts, or sheet metal components, we’re here to help you make the best choice between 304 vs 316 stainless steel—based on real usage, not just datasheets.
Conclusion
Choosing between 304 vs 316 stainless steel isn’t just about specs—it’s about matching the right material to the right environment. Whether your priority is cost, corrosion resistance, or long-term durability, understanding the differences ensures better results and fewer risks. For expert guidance and reliable production, we’re here to help.